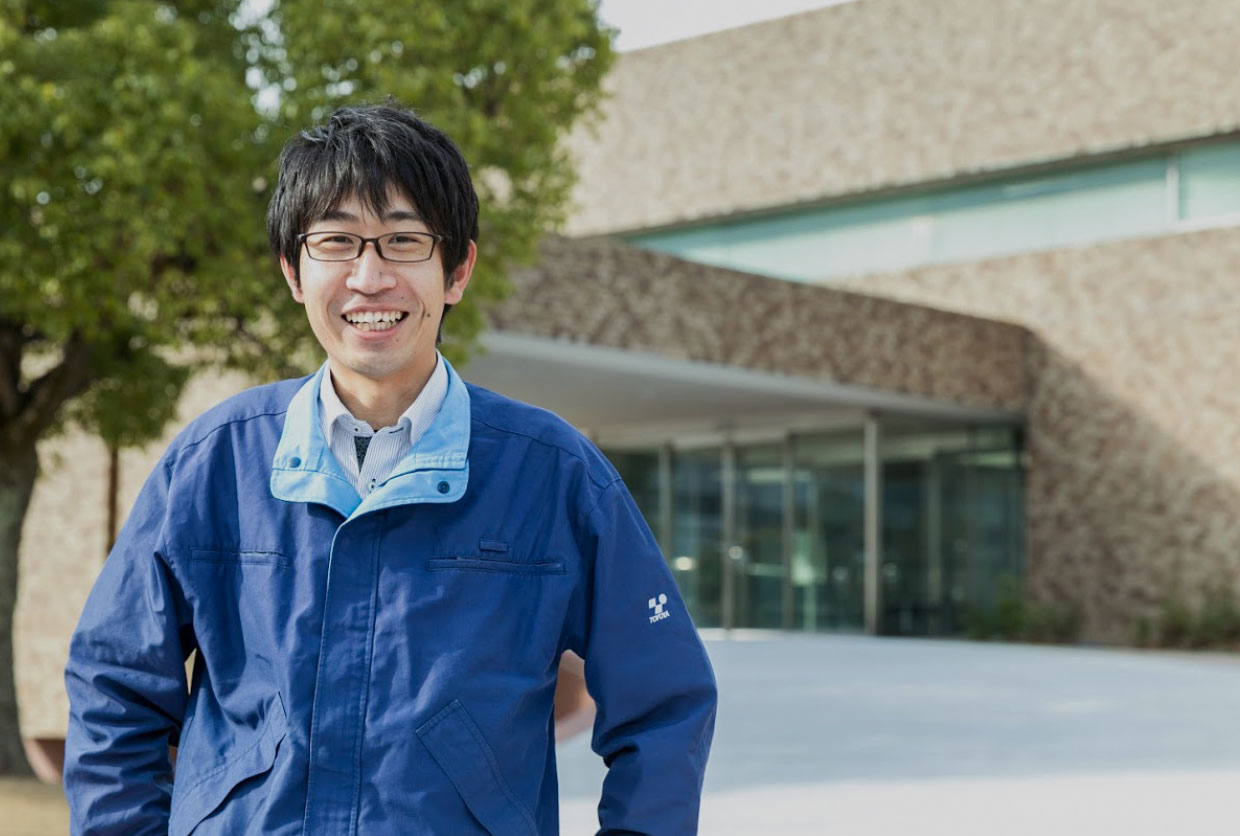
- 技術総合職
エレクトロニクス事業部 技術部
2011年4月入社
工学部卒
村山 陽一
BEV市場拡大に伴い、
ニーズが高まる車載充電器。
更に環境性能を高める
設計を目指して。
PROFILE
電気自動車の普及が進む中、車載充電器の開発に従事
入社後は集合研修に参加し、その後エレクトロニクス事業部の配属に。以来、車載充電器の開発業務に携わっています。当初はそれほどでもありませんでしたが、この10年の間に、各車両メーカーから電気自動車やプラグインハイブリッド車が登場し、それに伴って車載充電器の開発競争も激化しています。お客さまからのニーズとしては「品質」「価格」に加えて、最近は「小型化」ニーズが高まっており、それらの要請に一つずつ、確実に応える製品を開発することが私たちの役割です。
MISSION
あらゆる環境・状況を想定した設計
車載充電器の開発を行う電源システム技術第2室において、主に電気系統のハード設計を担当しています。さまざまな環境で使用される車載充電器は、使用状況を想定し、あらゆる条件に耐え得る設計を行うことが重要です。例えば、常温で問題なく動いても、高温になると不具合が生まれてしまう状態は、多くの人の移動を支える製品において、決して許されることではありません。そのため、いかに「検証」を徹底するかがカギとなり、机上計算、シミュレーションで確実に問題をつぶし、その上で試作品を用いて評価を行っていきます。その過程においては相当の時間とコストを費やしているため、実際に試作品を動かして評価を行う時は今でも緊張します。狙い通りの結果が得られればひと安心。万が一問題が発生すればただちに要因を追究し、再度設計に立ち返って問題の再発防止を実施。初めからすべてを設計に落とし込むのは困難ですが、1回目の試作品から高品質な製品を作れるように挑戦する日々が技術者としての成長につながっていると感じています。
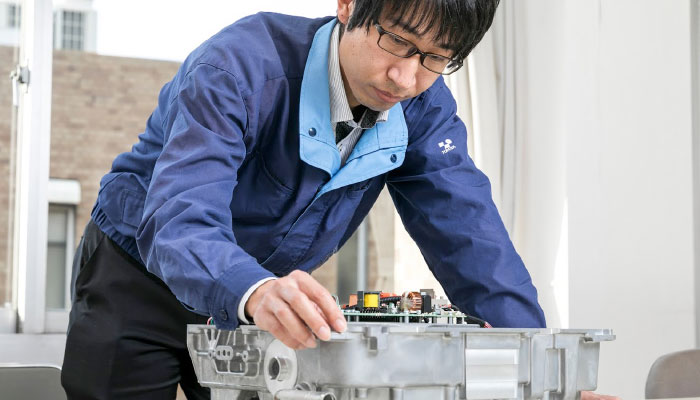
EPISODE
真因にたどり着くまで妥協はしない。
それがショッキのプライド
以前、開発中の試作品で許容範囲を超え温度が上昇し続けたことがありました。冷却機能の問題なのか、充電器を構成する部品自体の発熱なのか、考えられる要因は大きく二つ。さらにそれぞれにおいて、いくつもの熱上昇の要因が浮かび上がりました。これらの要因を全て検証していくのは膨大な作業になりますが、グループメンバーや部品メーカーの力を借りて、熱上昇の要因を一つずつ地道に洗い出し、検証することに。数週間かかって要因を特定し、無事に対策を打つことができました。
ショッキでは問題を引き起こしている真の要因を「真因」と呼んでいるのですが、この真因の特定こそが何よりも大切で、何としても成し遂げなければならないミッションでもあります。「これが要因だろう」と対策を行い、結果的に熱上昇が安定したとしても、実はたまたま抑えられたように見えているだけ、ということが実際にはあり得ます。真因にたどり着くまで可能性を洗いざらい検証する。そこには、品質に責任を持つショッキの技術者としてのプライドがあるのだと思います。
DREAM
製品の不具合でお客さまを裏切らないために
電気自動車の普及に伴い、私たちの手掛ける車載充電器も非常に多くのお客さまにご利用いただいています。その一方で、たった一つでも性能を損なう製品を市場に出せば、お客さまの信頼を失い、大きな影響を及ぼすことも事実です。だからこそ、あらゆる角度からシビアに評価を行い、「絶対に大丈夫」と言える製品を世の中に送り出すことを目標にしてきました。この思いは担当する製品が変わったとしても、これからも変わることのない私の信念とも言えます。
入社から主にハード設計に携わり、初期の開発から量産するまでの流れを一通り経験してきましたので、今後はお客さまと仕様を調整し開発のかじ取りを行う主担当を目指していきたいと考えています。多くのメーカーが参入し競争が激化する中においても、これまで以上に技術開発をリードできるよう、スキルの向上に努め、世界中の人々の豊かな生活・温かい社会づくりに貢献していきます。
VISION 2030
充電スタンドからクルマへ電力を送る際に発生するロスを、いかに削減し、高効率な充電器を開発できるかがテーマ。効率100%はまだ実現できていませんが、より高効率な電力供給を行える、環境に優しい車載充電器を作っていきたいと考えています。
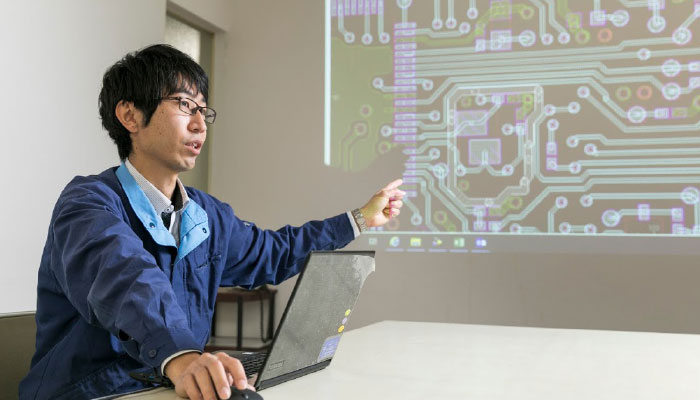
SCHEDULEとある1日のスケジュール
-
9:00
メールチェック・スケジュール確認メールの返信、業務の優先順位確認。
-
9:30
回路設計初期バラツキや温度特性を含めた回路の成立性確認。
-
11:30
会社の食堂で昼食コロナ対策で時差喫食対応中。コロナ禍前は同期と話しながら食べていました。
-
12:30
グループ内情報共有会各グループメンバーの進捗共有、業務負荷調整、課題に対する方針決めやアイデア出しをしています。
-
14:00
信頼性評価内容すり合わせ信頼性評価条件が客先要求を満たしているか関係者で確認。
-
15:00
部品メーカーと打ち合わせ次回試作時の部品仕様と納品日程についての打ち合わせ。
-
16:00
基板パターン設計次回試作の基板パターンや部品配置を専用ソフトを用いて設計。
-
18:30
設計変化点影響確認会設計変更による製品への影響をグループ内でレビューして確認。
-
19:30
翌日のスケジュール確認、業務整理。一日の業務進捗の整理、翌日の業務を確認。
-
20:00
帰宅