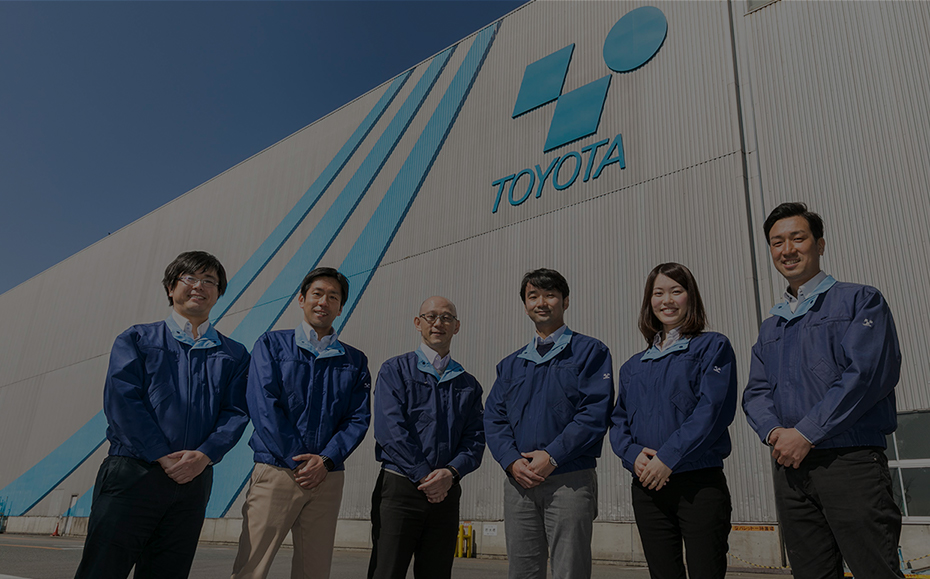
自動車
長草工場 新生産ライン立ち上げ
かつてない挑戦の中で、
数々の新たなアイデアを導入。
MEMBER
-
自動車事業部
生産技術部
武藤 大作 -
自動車事業部
生産技術部
高橋 宣也 -
自動車事業部
生産技術部
田中 克幸 -
自動車事業部
生産技術部
小澤 知子 -
自動車事業部
生産技術部
宮谷 憲太郎 -
自動車事業部
生産技術部
髙森 朗
STORY 1
「ランニングチェンジ」への挑戦。
世界的にヒットし、日本カー・オブ・ザ・イヤーも獲得したトヨタのRAV4。掲載中のプロジェクトストーリー「RAV4の製品企画・デザイン・設計・評価」では、その革新的なデザインの実現に挑んだメンバーたちの奮闘を紹介した。
実は、豊田自動織機のRAV4にまつわる挑戦はそれだけではない。生産ラインの構築においても、かつてない挑戦が展開されていた。
舞台は、愛知県大府市にある長草工場。本プロジェクトによって完成した生産ラインは立ち上げ後、世界各地のトヨタグループの拠点から「生産ラインを実際に見たい」「どうやって実現したのかを聞きたい」と視察が訪れるほど注目を集めた。どこにそのようなインパクトがあったのか。キーワードは3つある。当時、プロジェクトのまとめ役を担った武藤にそれぞれ解説してもらおう。
1つ目のキーワードは「ランニングチェンジ」。
「本プロジェクトでは、それまでヴィッツを造っていたラインを、新型RAV4を造ることのできるラインに改装しました。小型車専用だったラインを、大きなクルマも造ることのできるラインへと全面的にリニューアルしたのです。こうした改装を行う際、一般的にはラインを数カ月間停止し、設備を入れ替える工事を行います。しかし私たちは今回、ラインの稼働をほとんど止めずに新たな生産ラインを構築する『ランニングチェンジ』を行いました。ゴールデンウィークと夏休みと年末年始、年3回の長期連休に少しずつ設備を入れ替え、3年かけて全部やり切る、という前例のない計画を立て、遂行したのです」
2つ目のキーワードは「元車(もとしゃ)工場」。
「プロジェクトスタート時点でRAV4は当社を含めて世界4カ国6工場で生産されることが決まっていました。長草工場はその中で最初に車両品質を造り込む『元車(もとしゃ)工場』を任されました。当工場がまず品質をしっかりと造り込むことで、他工場も品質の高い車両を造ることができる。そのような責任重大な役割を私たちは担うことになりました」
3つ目のキーワードは「SEQCD競争力」。
「製造工程におけるSEQCD(Safety=安全、Environment=環境、Quality=品質、Cost=コスト、Delivery=納期)の優位性をどうすればより強化することができるか、各工程において知恵を絞り、新たなアイデアを導入しました」
ここまでがプロジェクト全般に関わる話である。Story2からは各担当の取り組みを紹介していく。各工程において、どのような挑戦が行われ、どのようなアイデアが導入されたのか。
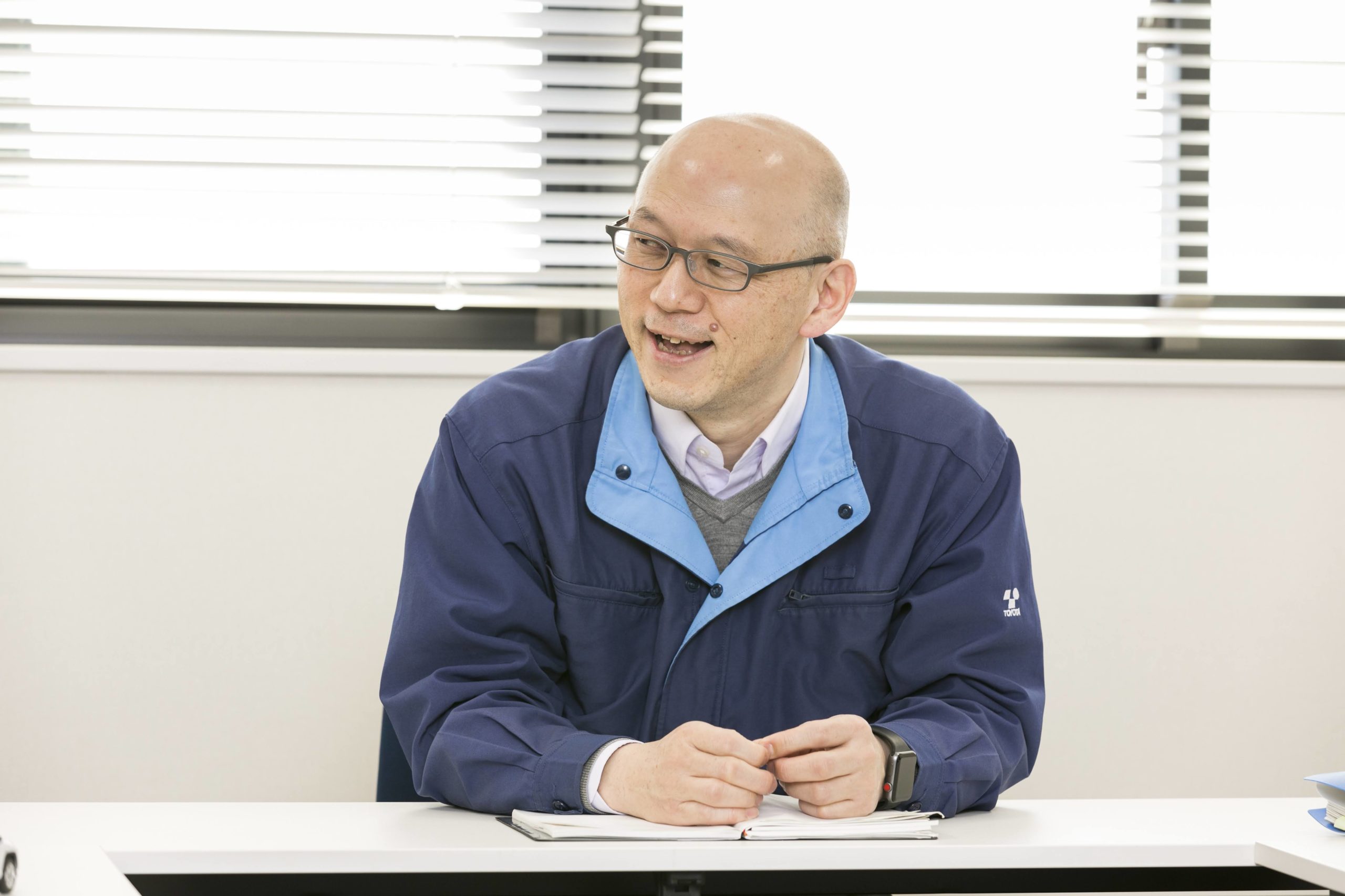
STORY 2
プレス工程:業界初のメカニズム解明に挑む。
プレス工程を担当した高橋は、品質不良の劇的な低減に挑んだ。
新型RAV4は軽量化を図るために、従来鉄を使用していたボンネット、バックドア、フェンダーの素材にアルミを採用した。アルミパネルのプレスは豊田自動織機初。高橋はその金型の作り込みを担当した。
実は、プレス工程担当にとってアルミはやっかいな素材である。
「アルミは鉄材と比較して、プレス時に品質不良が出やすいのです。原因は、切りくず。材料を金型で切断する工程で微細な切りくずがどうしても発生してしまい、それが不良率を高める原因になっていることが事前調査で分かりました」(高橋)
そこでプレス工程チームは、切りくずが発生するメカニズムを徹底的に追究した。
「実験用の金型を製作し、アルミパネル切断時の様子を高速度カメラで撮影して分析しました。その結果、プレス加工業界で初めてアルミ切りくずの発生メカニズムを解明。切りくずを出さない新工法を開発し、金型に織り込みました」(高橋)
さらに念を入れて切りくずが発生した場合も想定し、トヨタグループ初の「切りくず吸引機」を考案して導入。新工法と吸引機の二段構えにより、低い不良率の実現に成功した。
「品質確保に向けて私たち生産技術部門と製造部門が一体となってあきらめずに取り組み続けたからこそ、結果として実を結んだのだと実感しています」(高橋)
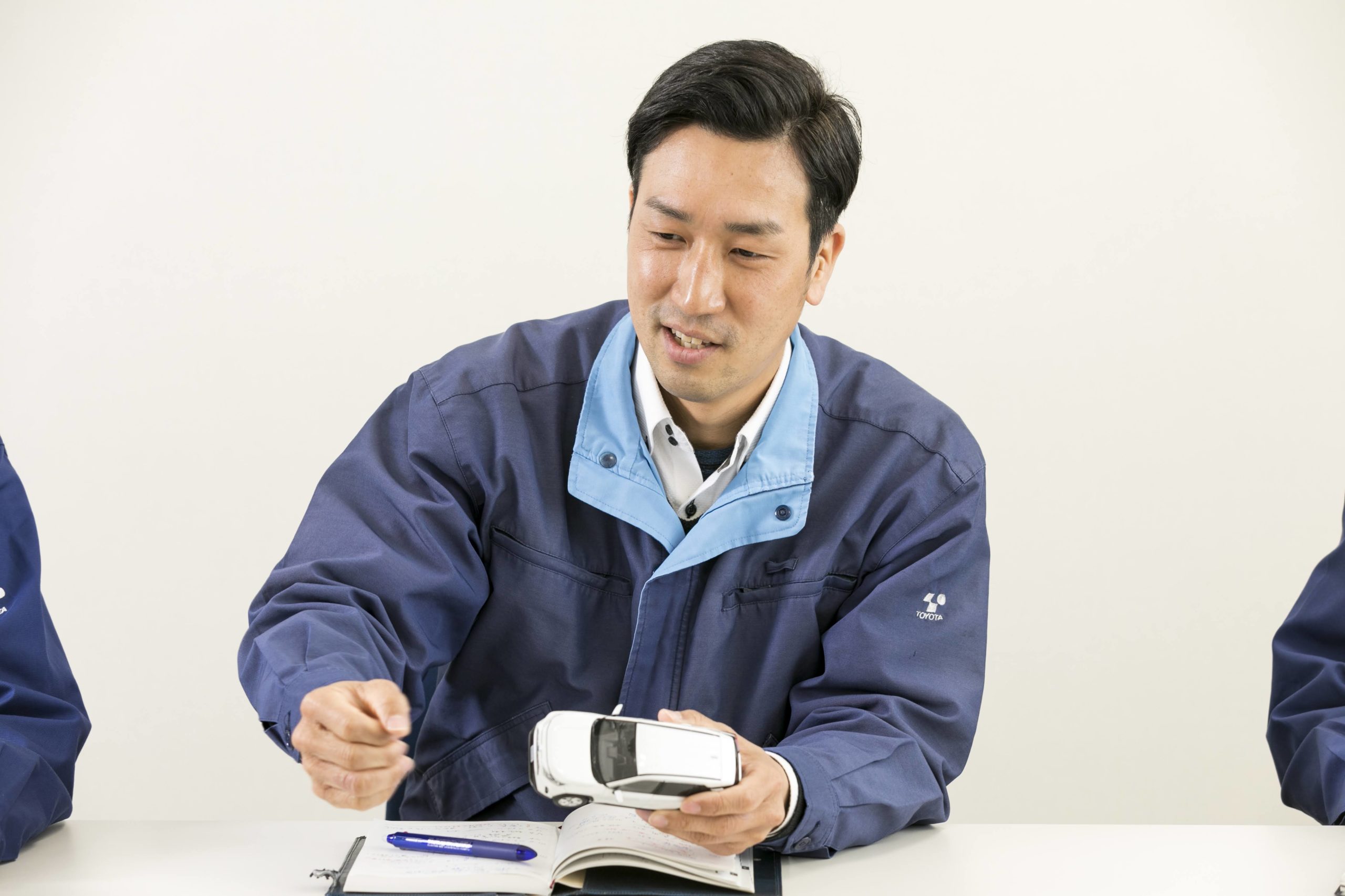
STORY 3
ボデー工程:既成概念にとらわれない着想
ボデー工程を担当した田中は「省スペースの溶接ラインを短期間で造る」という課題の解決に知恵を絞った。
これまで小型車を生産していた狭い工場に、サイズアップした車両の溶接工程を造らなければならない。しかも、連休中に移設工事を完了するという条件の中で。
「この難問に頭を悩ませていた時、ふと息子が遊んでいたスライドパズルを見ていて『これだ!』とひらめいたんです」(田中)
15枚のピースを縦横にスライドさせて数字を揃えるスライドパズル。田中はそこから着想を得て、パレットを前後左右に平面入れ替えする方式で搬送する設備を考案した。
従来の溶接ラインは6工程の構成。上段でワークを溶接し、下段で空パレットを返却する搬送方式だった。田中の考案したスライドパズル方式は工程数を従来の半分である3工程にし、スペース4割削減を実現。しかも従来の方式ではピットと呼ばれる穴を掘る必要があり、数カ月の工事期間が必要だったが、スライドパズル方式ではその必要もなく、設置工期のミニマム化も達成することができた。
「難しい制約の中でのプロジェクトでしたが、だからこそ既成概念にとらわれずに、従来にない生産設備を考案し、実際に形にすることができました。私は新しい生産ラインを造るとき、必ず何か一つは新しい発想を取り入れることを心がけています。新たな挑戦に積極的に取り組める風土が当社の大きな魅力の一つだと実感しています」(田中)
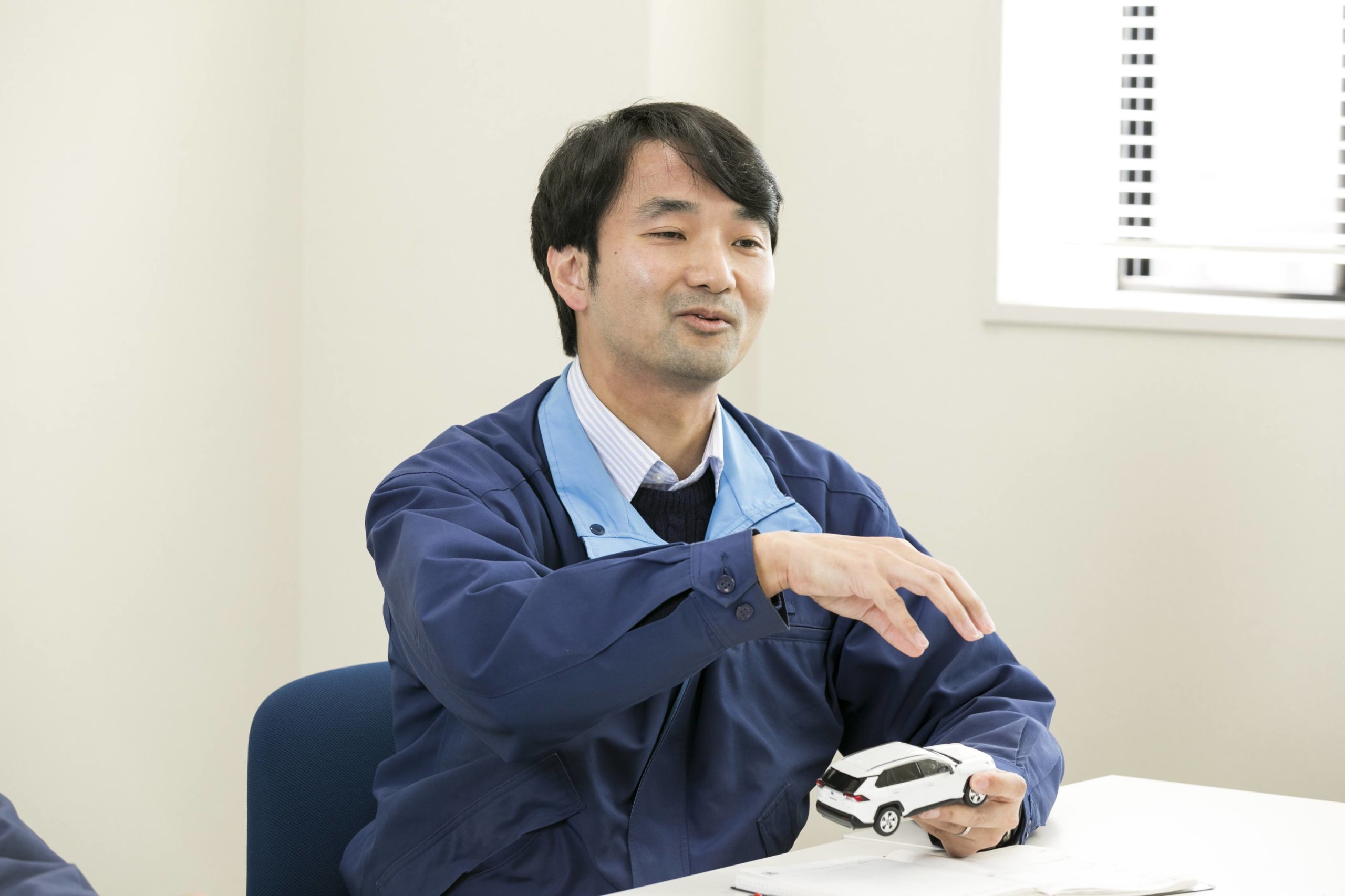
STORY 4
成形工程:不可能と言われていた技術を確立。
成形工程を担当した小澤は、当初不可能と言われていた技術を確立するために奮闘した。
バンパーは金型に樹脂を流して成形する。今回、大型化するバンパーを効率よく生産するために、2つの部品を1つの金型で同時成形する「ファミリーモールド成形」を採用した。
「ファミリーモールド成形そのものは、既存の技術です。今回の難しさは、体積が従来と比べて約2倍だったこと。体積が大きいと金型が射出中に開いて樹脂がはみ出し、品質が確保できなくなってしまうのです。当初は不可能ではないかという声もありました」(小澤)
成形工程チームはあきらめずにコンピュータ上でシミュレーションを繰り返した。そして金型上での製品配置やゲート(樹脂を流す入り口)配置の最適化を図り、安定供給できる技術の確立に成功した。
小澤は配属1年目でこのプロジェクトに参画。金型の造り込みと成形工程の整備を行った。
「フロントバンパーはデザイン上、クルマの顔を構成する部品。デザインチームは『詳細な曲率一つにも意味がある』と強いこだわりを持っています。今回のデザインは成形工程チームにとっては難しいものでしたが『できる限り粘って、何とか実現したい』という思いで取り組みました」(小澤)
当時も今も、小澤は人とのつながりを大切に考えている。
「たくさんの部署の方々と、みんなで一丸となって愚直に品質向上に取り組んだことで目標を達成できました。部署の垣根を越えたチームワークは、豊田自動織機の強みだと確信しています」(小澤)
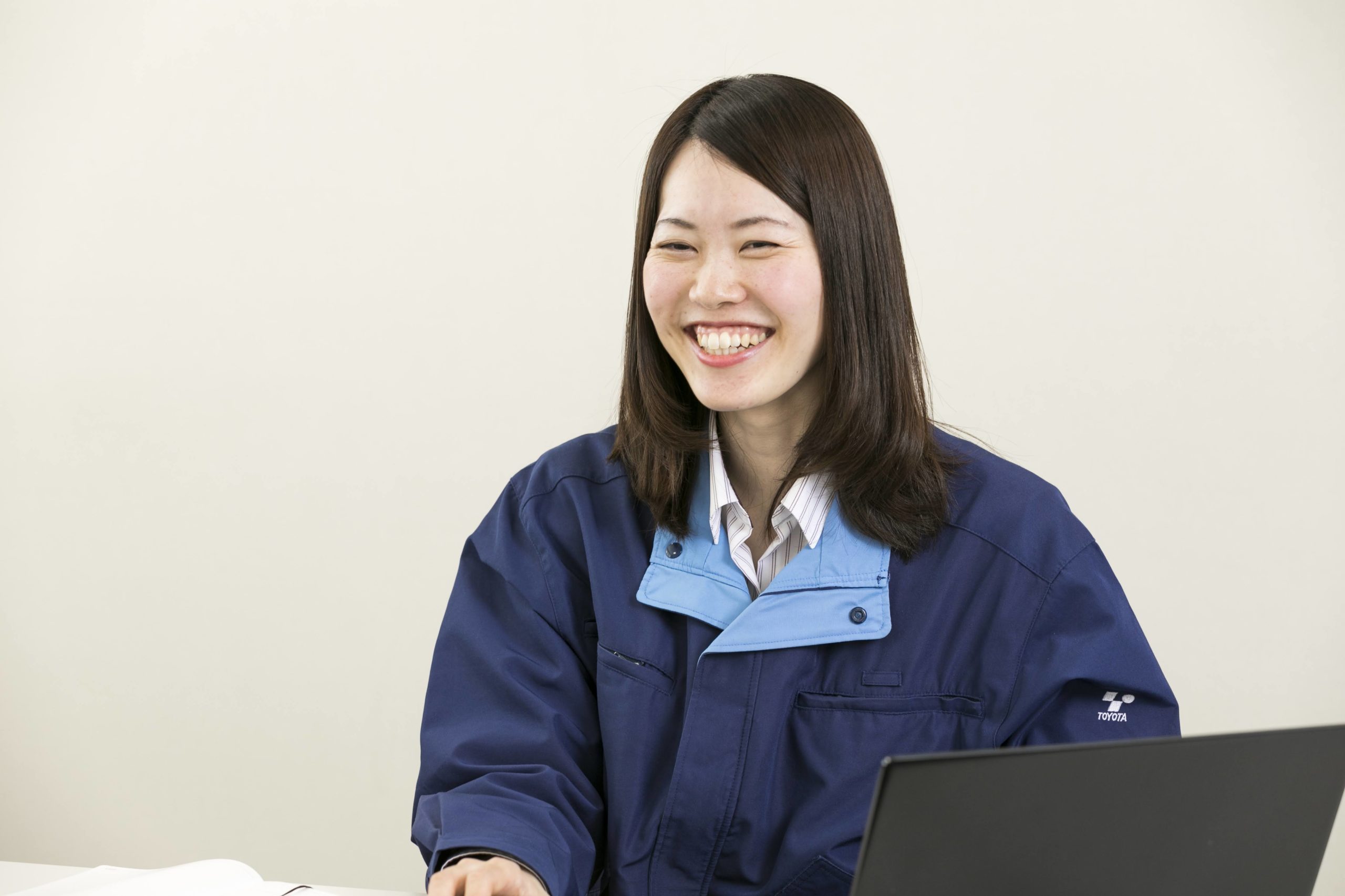
STORY 5
塗装工程:工場稼働を継続させながらの改装で大幅なCO₂排出量削減を達成。
塗装工程を担当した宮谷は、「全てがチャレンジだった」と振り返る。
塗装工程は他の工程に先行して改装工事に着手。工場を稼働させながら、4年以上にわたって途切れることなく、平日や土日、連休に設備切替工事を行った。
宮谷はスタート時から「電着」と呼ばれる表面処理工程の設備更新を担当。その後、長草工場内2ラインへの新型RAV4導入における塗装工程の責任者を務めた。
「狭い工場内でのランニングチェンジは、世界中の車両生産工場を見渡しても前例のないこと。やり切るにはどうしたらよいかをみんなで考え抜き、他にはないアイデアを絞り出しました。例えば、平日に車両を生産しながらその真下で重機で床を掘削するような工事も実施しました。
その中で、CO₂の大幅削減技術やグループトップレベルの工程品質を目指し、達成することができました」(宮谷)
塗装工程には、塗料を車両に定着させるために乾燥させる「乾燥炉」という設備がある。今回の更新を機に熱ロスを低減する工夫を取り入れた乾燥炉を導入し、大幅なCO₂削減を達成した。その取り組みが評価され、一般社団法人省エネルギーセンター主催の省エネ大賞(省エネ事例部門)において、最高賞である経済産業大臣賞(産業分野)を受賞した。
「一緒に仕事をしたメンバーが受賞したのはとてもうれしく、誇りに思います。これからもより良いクルマづくり、環境にやさしい工場づくりに貢献していきたい。私たちのチャレンジはこれからも続きます」(宮谷)
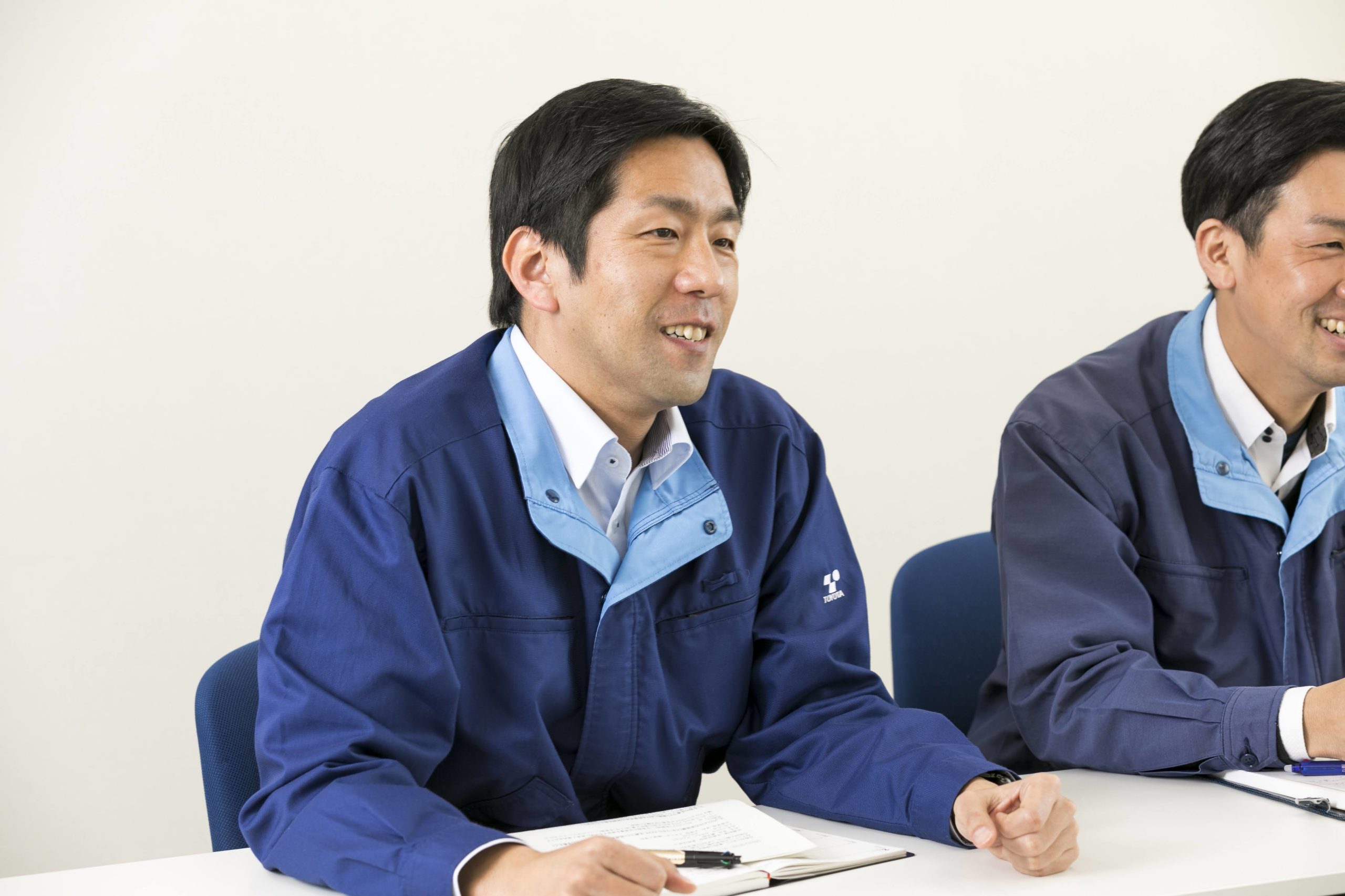
STORY 6
組立工程:現場と共に最善の造り方を追求。
組立工程を担当した髙森は、製造現場と一体となり、より働きやすいラインを造り上げた。
「組立は製造プロセスにおける最後の工程。もし設備が停止してしまうと生産台数に直結します。切り替える際には立ち上げ後に稼働を落とすことがないよう、事前に工程の完成度を高めておくことが非常に重要です」(髙森)
工程の完成度を高める、と聞くと、設備に対する取り組みをイメージするのではないだろうか。しかし組立工程の場合は「人を含めた工程の完成度を高めることが重要」と髙森は語る。
「組立は、人と設備が共存する工程です。本プロジェクトでは実際のラインを設置する前に別の場所に設備を再現し、製造現場の皆さんの声を聞きながら作業訓練・設備改修・改善を実施。工程をしっかりとつくり込んでいきました。私たち生産技術と製造部門は一つのチーム。綿密に連携しないと、良いモノは造れません」(髙森)
工程のレイアウトを見直して物の流れる動線を最短化する、作業者の後ずさり作業をなくして負担軽減に貢献できる設備を導入する、など、生産技術のメンバーは製造部門の思いを取り入れながら最善の造り方を追求した。
また、髙森は元車工場としての活動にも積極的に取り組んだ。
「私たちの後に生産ラインを立ち上げる拠点に、車両特有の注意すべきポイントを伝える活動を行いました。この活動は後続の拠点から『非常に助かりました』と評価いただきました。トヨタ自動車のカナダ工場を視察する機会も得られ、生産準備のエンジニアとして貴重で有意義な経験を積むことができたプロジェクトでした」(髙森)
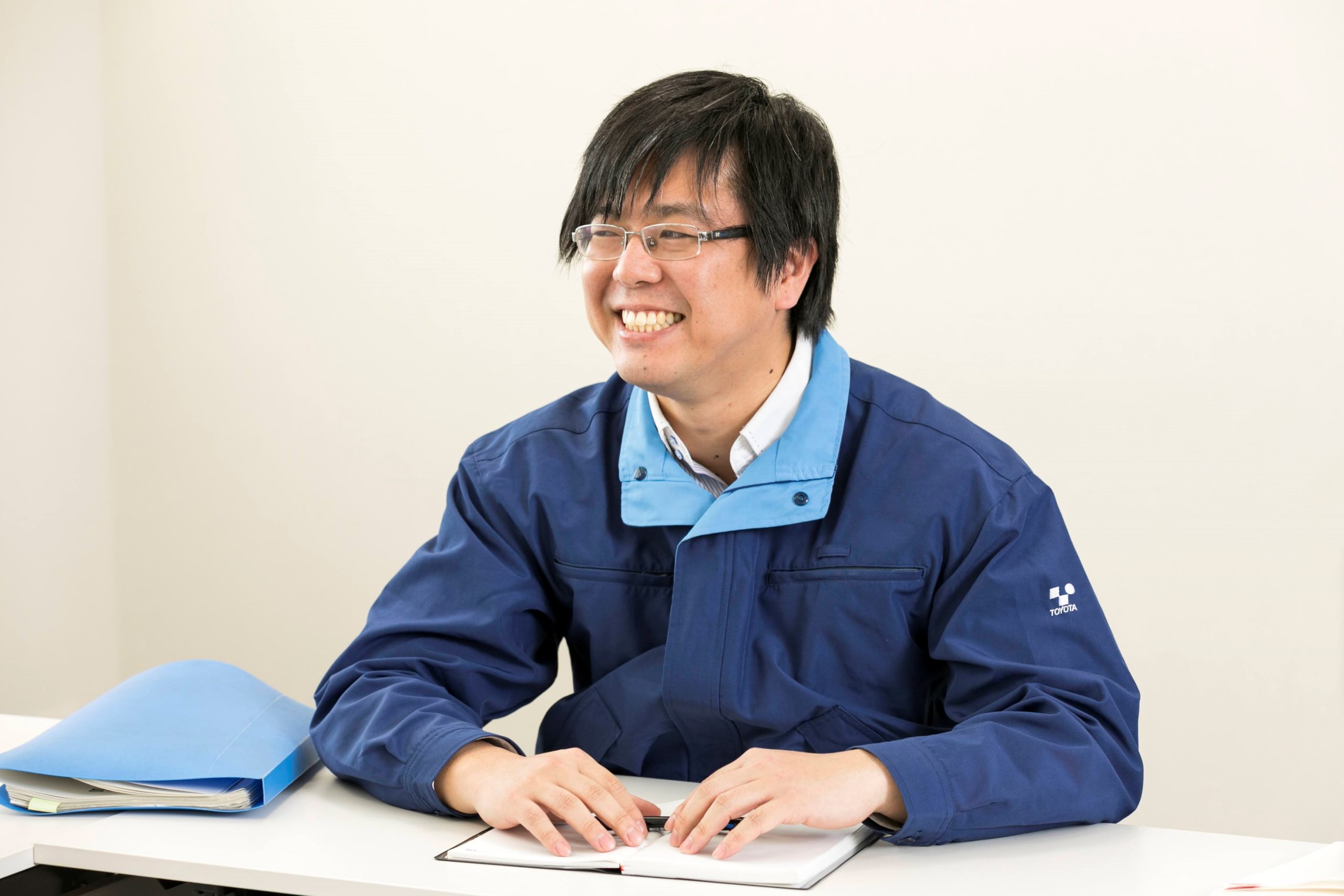
STORY 7
一人一人に根付いている豊田綱領。
プロジェクトメンバーたちは、前例のないランニングチェンジをやり遂げた。ラインオフ式には、トヨタ自動車の副社長をはじめ、販売店、仕入先、豊田自動織機従業員の代表者約350人が出席。式典の中で豊田自動織機の大西朗社長は「グローバル戦略車にふさわしい品質の車を、ここ長草工場から世界中のお客様にお届けしたい」と抱負を述べた。
その言葉通り、今、RAV4は世界中のお客様に届けられている。また、このプロジェクトの中で生まれたいくつかの新たなアイデア――製造工程の安全性を高める、環境負荷を低減する、品質を高める、コストを削減する、効率を高めるアイデア――は、トヨタ自動車のさまざまな工場で採用されている。
豊田自動織機には、社是として社員のよりどころとなっている、豊田綱領がある。
(企業理念ページはこちら→)
「今回のプロジェクトにおいても、豊田綱領の価値観がいかんなく発揮されました。ただ、豊田綱領を意識して取り組んだと言うよりは、この価値観は豊田自動織機の一人ひとりに自然に根付いている、と言った方が、しっくりきますね。昔から培われた土壌になっている。だからこそ今回の前例のない挑戦も達成できたのだと実感しています」(武藤)
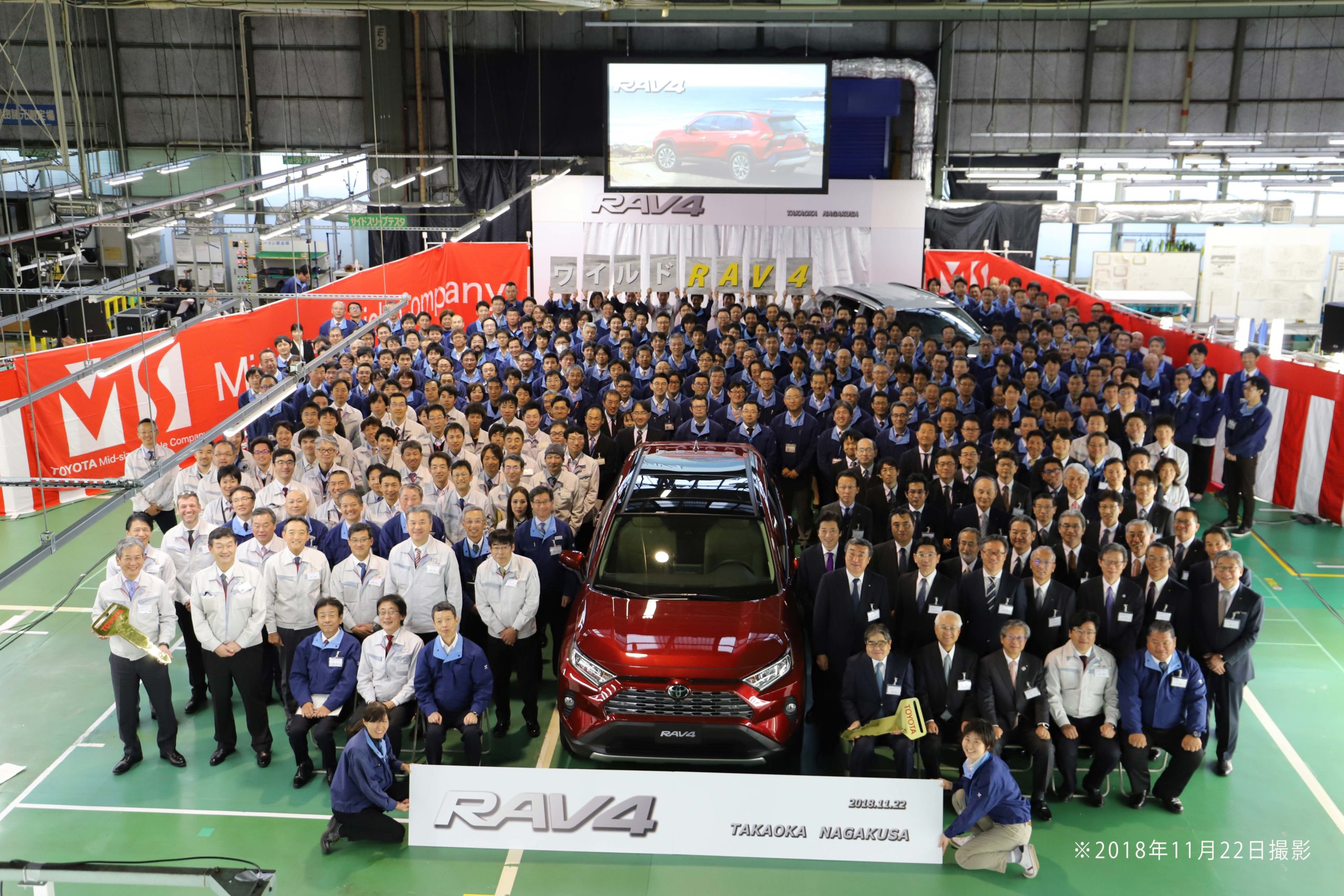