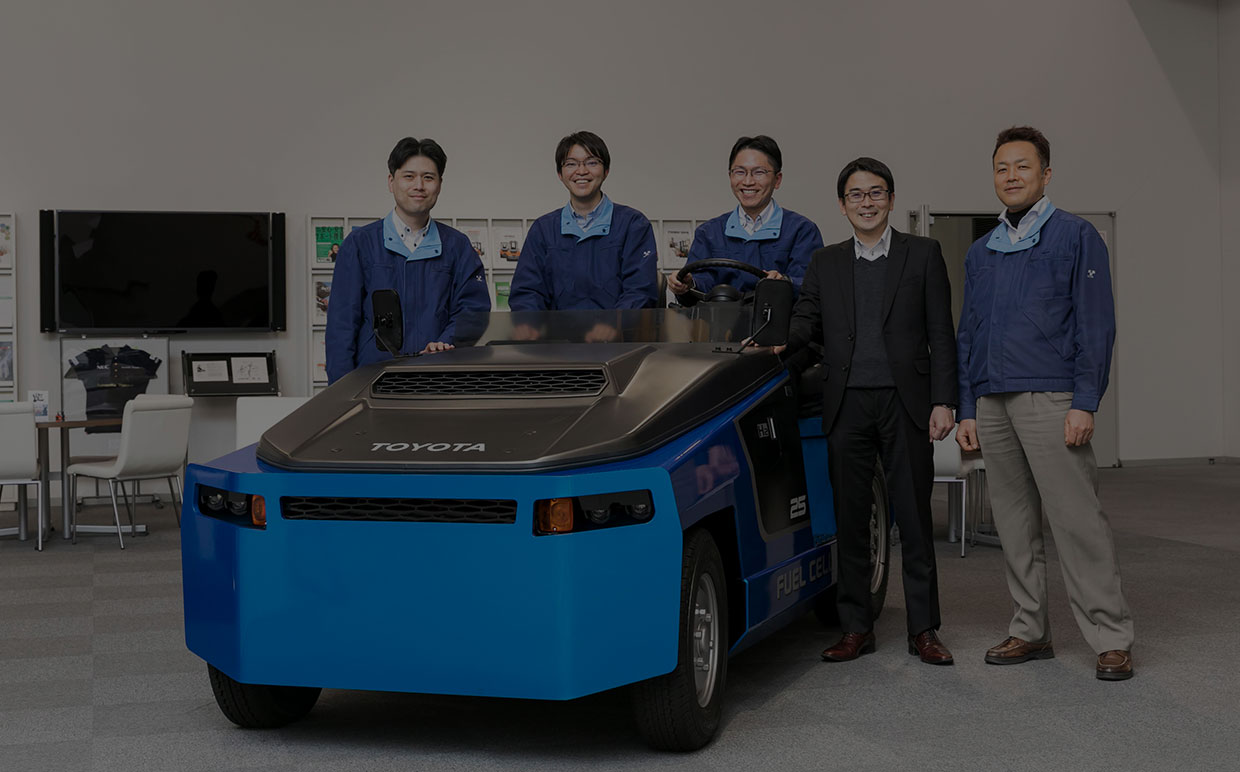
産業車両・物流
燃料電池トーイングトラクター開発
不可能を可能に変えた、
チーム間の「相互理解」。
MEMBER
-
トヨタL&Fカンパニー
R&Dセンター
ARプロジェクト
佐藤 誠 -
トヨタL&Fカンパニー
R&Dセンター
ARプロジェクト
西尾 潤 -
トヨタL&Fカンパニー
産車用FCプロジェクト
小林 健人 -
トヨタL&Fカンパニー
H2プロジェクト
下簗 祐介 -
トヨタL&Fカンパニー
H2プロジェクト
立花 将規
STORY 1
「日本初のFCフォークリフト」から次の展開へ。
日本を含む世界各国で「2050年カーボンニュートラル」への取り組みが進められる中、注目を集めている燃料電池(以下、FC)技術。それは豊田自動織機が長年にわたって追究し、蓄積してきた技術でもある。
豊田自動織機がFCを搭載した産業車両の開発に挑み始めたのは、2000年代初頭のことだ。リーマンショックの影響で開発体制の存続が危ぶまれた時期もあったが、エンジニアたちが開発の灯を絶やすことはなかった。そして十数年間にも及ぶ開発期間を経て2016年、ついに日本初のFCフォークリフトの販売を開始。その後、環境性能の高いFC製品のさらなる普及のために、新たな用途への展開を模索していた。
そんな中、注目した場所が空港だ。
空港は多種多様な産業車両やバス・トラックが24時間稼働しているため、水素利活用の一大集積地となるポテンシャルを持っている。そして、飛行機を除くと空港において、最も多くのCO₂を排出しているのはトーイングトラクターだといわれている。
トーイングトラクターとは、貨物を搭載したコンテナをけん引する産業車両。一つの空港当たり、数百台単位の車両が終日走り続けている。エンジン式と電動式があるが、欧州を除くとエンジン式が主流となっており、それだけにFC車が普及したときのCO₂削減効果は大きい。また、電動車は台数によっては広い充電スペースを必要とし、充電にも時間を要するが、FC車ではそういった課題をクリアできる強みもある。
こうした背景からFC技術の新たな展開として、FCトーイングトラクターの開発がスタートした。
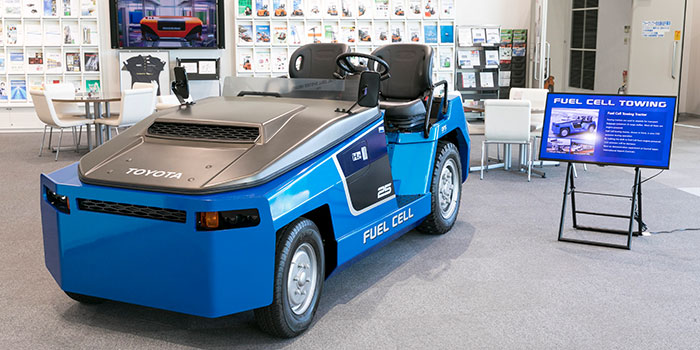
STORY 2
電動車とFC車で大きく異なる点。
トーイングトラクターは、豊田自動織機において長い歴史を持つ商品の一つでもある。1956年にエンジン式、1981年に電動式の商品を販売開始した。
FCトーイングトラクターの開発に当たっては、直近に発売された電動車をベース車両として選定。また動力源のFCユニットは、FCフォークリフトに搭載したものをベースに開発が進められた。
ただベース車両にFCユニットを搭載してFCトーイングトラクターは完成――というわけにはいかない。電動車のFC化は、実はそれほど単純なものではないのだ。
「電動車とFC車で大きく異なる点が、排熱です」。そう解説するのは、FCトーイングトラクターの車体設計を担当した佐藤。FCフォークリフト開発プロジェクトにおいても車体設計に携わっており、電動車のFC化は既に経験済み。ポイントとなる箇所についての知識は有していた。
「FC車では車両側面にFCユニットの排熱のための開口部を設ける必要があります。フォークリフトの場合は該当箇所が意匠部品だったので、開口部を設けることに対して強度的な問題はありませんでした。しかしトーイングトラクターの場合は該当箇所に強度部材があり、開口部を設けるにあたり強度を確保するための工夫が必要です。開発が本格化する前は、そこが課題になりそうだとイメージしていました」(佐藤)
しかし開発が進むにつれ、その課題は数ある難題の一つに過ぎなかったことを、佐藤は痛感することになる。
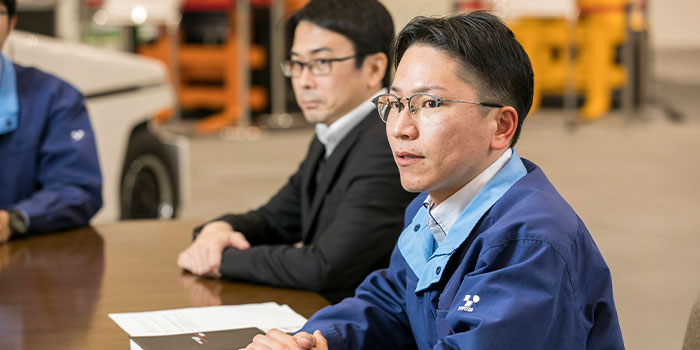
STORY 3
水素タンクを増設したい。
トーイングトラクターには連続して長時間稼働のできる性能が求められる。難題の一つは「連続稼働時間をいかにして伸ばすか」だった。
佐藤はFCユニット開発チームに「1回満充填をしたときに、エンジン車同等に連続で稼働できるようにしたい」と要求を出した。要求を受け、FCユニット開発チームは検討を重ねる。その結果、導き出されたアイデアは、佐藤にとって思いもよらない内容だった。
「『水素タンクを1本追加し、2本搭載したい』と提案したんです」――そう語るのは、FCユニットの開発リーダーを務めた下簗だ。
「目標値を達成するには、搭載可能な水素の量を増やす必要があります。しかし車両の横幅は決まっているため、水素タンクを長くすることはできません。かと言ってタンクの直径を広げるにも限度があります。ならば搭載レイアウトを工夫しタンクを1本増設するしかない、という結論を出しました」(下簗)
このアイデアによって連続稼働時間の課題は解決の目処が付いた。しかし追加する水素タンクをどのように取り付けるか、という新たな難題が生まれた。それだけではない。排熱の課題も、想像以上に高い壁となって立ちふさがった。
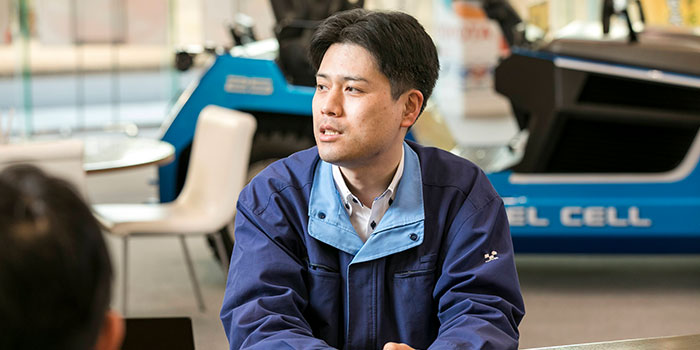
STORY 4
「絶対に無理」と若手エンジニアは言った。
「トーイングトラクターに必要なけん引力を達成するため、FCユニットの出力をフォークリフトのものから約2倍に高めています。そうすると発熱の量も約2倍になるんです」(下簗)
2倍になった発熱量に対し、どのような冷却システムを構成するか。この難題に挑んだのが、当時入社3年目の立花だった。
「本当に苦労しました。今でも鮮明に覚えていますが、一度上司に直談判したんです。『この目標性能の実現は、絶対に無理です』と」
目標性能は、現場でどのように使われるかで決まる。トーイングトラクターは稼働時間や走行距離が長く、真夏の屋外での走行も想定しなければならない。冷却システムに要求される性能は高い。
「ラジエータを大きくしようにも、搭載スペースの制約で限界があります。条件を考慮すると提示された目標性能は、どう計算しても成り立たない。あまりにも無理がある。私にはそうとしか思えませんでした」(立花)
しかし、上司の答えを聞き、立花は考えを大きく変えた。
「私の主張を聞いて上司はこう言いました。『不可能であれば、自分で理由を突き詰めて、どこに問題があるのかを考えるんだ。その上で実現できる方法を見つけて解決するのがエンジニアの仕事だ』と。この言葉を聞いて、自分の視野の狭さに気付きました。これまで与えられた目標値ばかりを見ていた。そうではなく、どうすればお客さまの要望をかなえられるかを考えなければ――そう考えを改め、再度検討を重ねました。その結果、『小型のラジエータを追加し、メインのラジエータをアシストする』という方法に行き着いたのです」(立花)
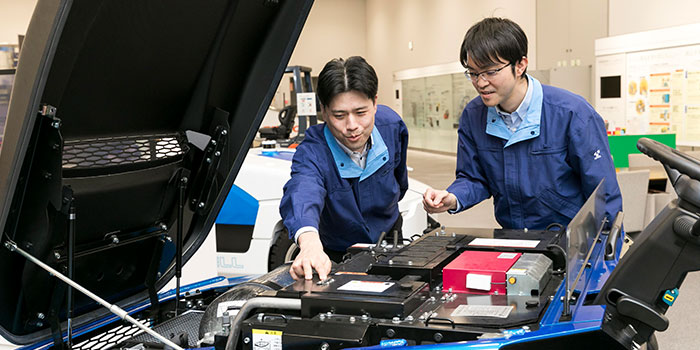
STORY 5
機能とデザインを両立させる。
水素タンクを2つにすることで連続稼働時間の課題を、ラジエータを2つにすることで排熱の課題を、それぞれ解決できる。しかし、これらを実現するには、まだ高い壁を乗り越えなければならない。2つ目のタンクとラジエータをどのように搭載するか、という課題が残されていた。
「元々の水素タンクとラジエータは、立方体のような形状のFCユニット内に全て収められています。その中にもう1つのタンクとラジエータを追加する空間はありません。必然的にそれぞれの2つ目はFCユニットの外側に取り付けることになります」(下簗)
大きさの制約を考えず、それぞれを運転席前方に位置するFCユニットの上部にポンと載せる、という話なら難しくはない。しかしFCユニット開発チーム・車体開発チームともに、運転席からの視界にできるだけ影響が出ない形で搭載したいと考えていた。
「限られたスペースの中でどのように取り付けるか、かなり悩みました。取り付けるためのフレームが振動実験中に折れたこともありました。計測データを見て原因を突き止め、対策案を考えシミュレーションで検証し、改良した部品を作り、試験する。どうすれば走行中の振動に耐えられるのか、試行錯誤を重ねました」(下簗)
車体開発チームも奔走した。
「水素タンクとラジエータの追加を実現するには、ボンネットの形状に膨らみを持たせる必要があります。しかし、ただ膨らませる、というわけにはいきません。デザインも商品性を左右する重要な要素ですから。機能とデザインを兼ね備えたシームレスな膨らみにするために、生産技術部と協業しました。インクリメンタル成形法という、金型を使わずに金属の薄板を自由な形状に成形できる工法があるのですが、今回はその中でもこれまでにない成形にトライしたんです。こうしてボンネットの機能上の膨らみとデザインを両立させることができました」(佐藤)
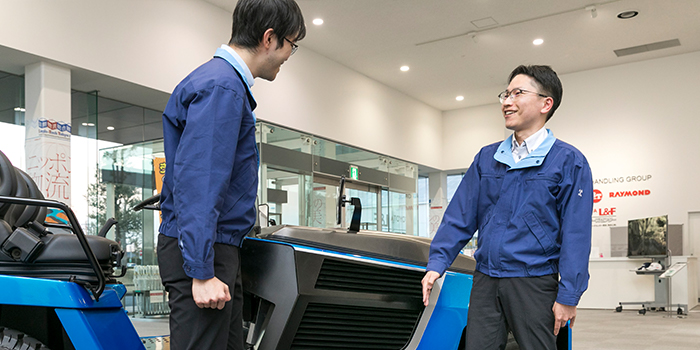
STORY 6
成功のポイントは「相互理解」。
1つの課題を解決しようとすると、新たな課題が現れる。その連続だったFCトーイングトラクターの開発。若手エンジニアが「絶対に無理」と感じたほどの難題も含め、数々の壁を乗り越えて車両は完成した。
なぜ乗り越えることができたのか。成功のポイントは「相互理解」だった。車体開発チームとFCユニット開発チームは、互いの要望を主張するだけでなく、互いが取り組む内容の理解に努めた。
「私たち車体開発チームも、FCユニットの構成や動作の理解に努めました。『水素タンクとラジエータをそれぞれ2つ載せたい』と聞いた時はとても驚きました。でも、FCユニットへの理解を深めることで、なぜ2つ必要なのかも分かるようになりました。互いの課題を定例会で出し合って理解していくことで、先手先手で課題解決に取り組むことができ、それが成功につながったのだと思います」(佐藤)
「開発に当たり、FCユニット開発チームのメンバーもトーイングトラクターの運転資格を取得しました。私たちの基本は、現地現物。机上だけで考えるのではなく、利用するお客さまの気持ちを自ら感じることが重要です。私も乗ってみて、視界の確保が重要だと自分自身で実感しました。水素タンクとラジエータを追加する際、視界をできるだけ狭めないことを考慮した載せ方で車体開発チームに提案したのですが、そこには自分が運転した時の経験も生きています」(下簗)
今回のプロジェクトでは車体開発とFCユニット開発を一貫して手掛ける豊田自動織機ならではの強みが、チーム間の相互理解によってより強く発揮された。
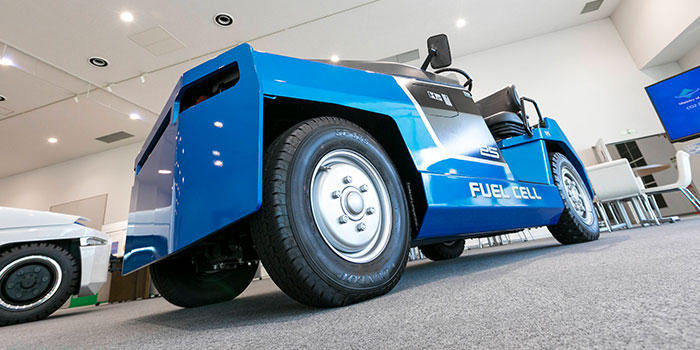
STORY 7
開発を支えた渉外活動。
ここまで技術面における取り組みを紹介してきたが、今回の開発を語る上で欠かせない取り組みが他にもある。それは渉外活動だ。
渉外活動とは、外部組織と連携・交渉すること。そもそもFCトーイングトラクターの開発プロジェクトは、環境省の「CO₂排出削減対策強化誘導型技術開発・実証事業」に採択され、補助金を得られたことがスタートを後押しした。
西尾はその採択に向けて環境省への技術渉外担当を務めた。
「FCフォークリフト開発の際にも同じスキームで開発補助を受けていました。さらなる水素利活用のための多用途展開の一環としてFCトーイングトラクター等の開発を提案することで有用性を認めていただき、再び実証事業に採択していただくことが出来ました」(西尾)
西尾は2000年代初頭に豊田自動織機がFC関連のプロジェクトを立ち上げた時から携わってきたメンバーの一人。その技術的なバックグラウンドを発揮し、環境省へのプレゼンテーションや開発の進捗報告を行った。
「この実証事業では特に『社会実装できるかどうか』が非常に重視されます。今回のプロジェクトでは『3カ年の最後に空港での実証実験を実現させます』とプレゼンしました」(西尾)
そして実際に3カ年の最後の年、中部国際空港での実証実験を開始することができた。その実現に向けて、中部国際空港株式会社やトーイングトラクターを運用する各グランドサービス会社への渉外活動に取り組んだのが小林だ。
「空港で実証実験を行う場合、保安制限区域というセキュリティ上、とてもシビアなエリアに車両を持ち込むことになります。また、私たち豊田自動織機社員もそこに入る必要があります。それだけに、空港側への車両・立ち入り者情報の提供や、水素ステーションの利用調整、その他実証実験中の取り回しの想定・相談など、事前の対応は多岐にわたりました。また、私自身は事務系の社員ですが、技術的な知識も頭に入れ臨んだことで、空港での車両や実験内容説明の際、先方からの質疑にも確実に対応することができました。綿密な事前準備に加え、中部国際空港が水素の利活用に積極的な空港であることも寄与し、交渉はスムーズに進みました。実証実験の立ち上げの際には、保安制限区域の中がどのような環境になっているかを見たり、実際に運用しているお客さまと話をする機会を得ることができ、今後につながる貴重な経験を積むことができました」(小林)
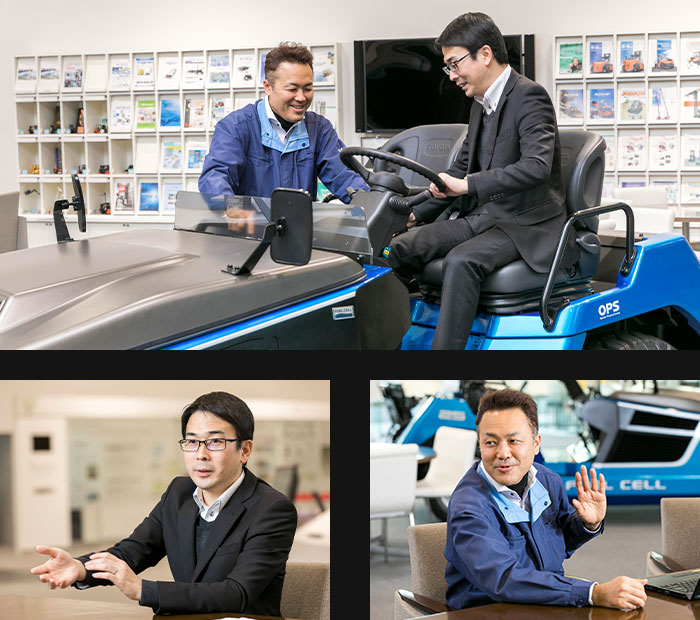
STORY 8
お客さまの望むモノを形にしていく。
豊田自動織機は、これからもFC技術のさらなる多用途展開を目指していく。FCユニット開発チームのメンバーは、今回のプロジェクトを通じ、技術面以外にも未来につながる大きな成果を得た。それは、意識の変化だ。お客さまの要望までさかのぼって開発要件に落とし込むことの大切さを、FCトーイングトラクター開発の成功が教えてくれた。
そうした意識の変化を象徴する立花の声をもって、このプロジェクトストーリーの締めくくりとしたい。
「お客さまの望むモノを、たとえ最初に実現不可能だと感じたとしても、何とか形にしていく。それがメーカーとしての使命であり、エンジニアとしての醍醐味であることを、この開発プロジェクトを通じて実感しました。水素への注目度が高まる中、これからもお客さま目線を大切にしながらFCの性能向上とコスト低減に取り組み、『2050年カーボンニュートラル』の実現に貢献していきたいと考えています」(立花)
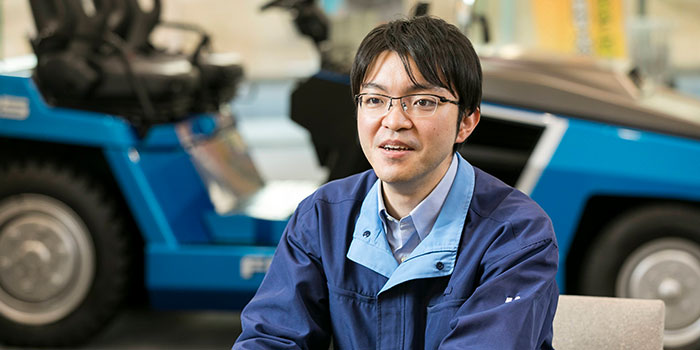