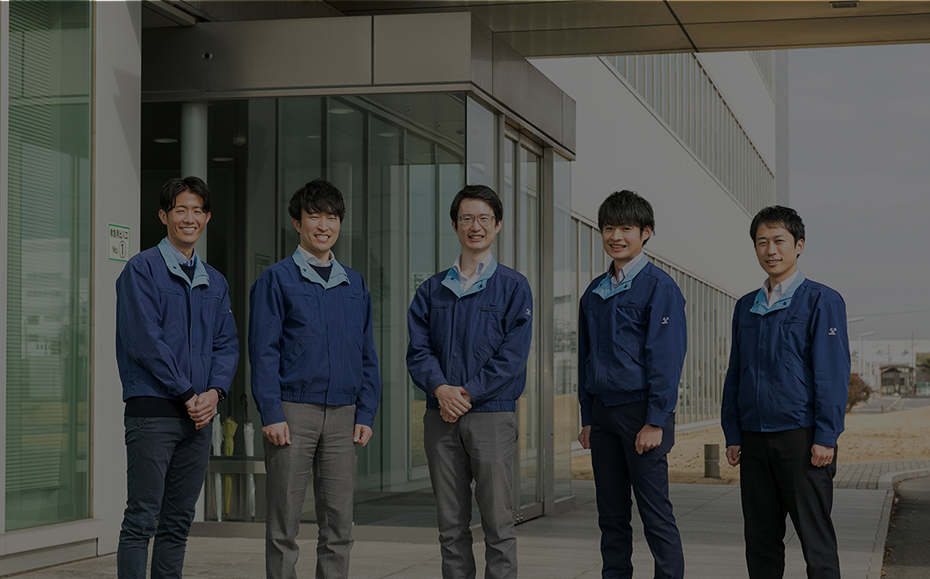
コンプレッサー
燃料電池自動車「MIRAI」搭載製品の開発
最先端で試行錯誤を繰り返し、
次世代をつくる。
MEMBER
-
コンプレッサー事業部
FCプロジェクト
渡辺 大祐 -
コンプレッサー事業部
FCプロジェクト
高荷 直樹 -
コンプレッサー事業部
FCプロジェクト
伊藤 正悟 -
コンプレッサー事業部
FCプロジェクト
篠田 史也 -
コンプレッサー事業部
FCプロジェクト
高瀬 陽平
STORY 1
高まる「究極のエコカー」への期待。
クルマ好きな方はもちろん、クルマのことはあまり詳しくない、という方も「MIRAI」という車名は知っているのではないだろうか。MIRAIはトヨタの燃料電池自動車(以下、FCEV)。このクルマには、豊田自動織機が開発した「エアコンプレッサー」と「水素循環ポンプ」という製品が搭載されている。
世界各国が気候変動問題に取り組み、日本においても2050年の脱炭素社会実現に向けた目標が掲げられている中、水素を燃料とし、走行時には水だけを排出するFCEVは「究極のエコカー」と呼ばれるほど期待が高まっている。
2014年に登場した初代MIRAIは、世界に先駆けて量産開始された革新的なFCEVとして注目を集めた。そして現在、FCEVのさらなる普及を見据えて開発された第2世代が販売されている。
第2世代が目指したのは「こんなクルマが欲しかった。それがMIRAIだった」と言っていただけるFCEV。初代と比較して航続距離が延び、スタイリングや走行性能なども見直された。その実現に豊田自動織機のエアコンプレッサーと水素循環ポンプも大きく貢献している。開発の過程でどのような困難に突き当たり、どう乗り越えたのか、プロジェクトメンバーたちに振り返ってもらおう。
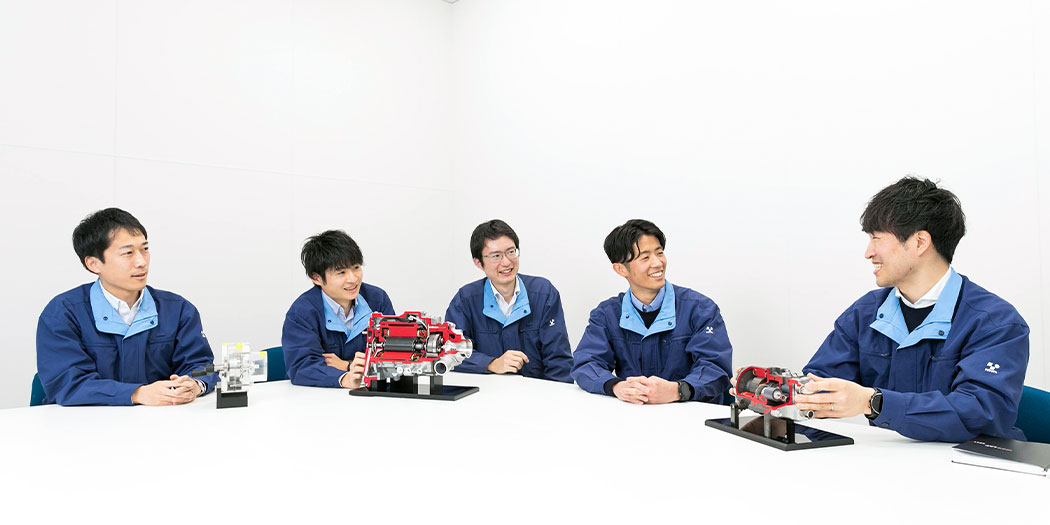
STORY 2
FCEVの走行に不可欠な製品。
メンバーの声を紹介する前に、FCEVの発電システムにおいてエアコンプレッサーと水素循環ポンプがどのような役割を担っているかを紹介しておきたい。
燃料電池は簡単に言えば「水の電気分解」と逆の化学反応を利用して電気を作る発電システム。FCEVにはFCスタックと呼ばれる発電装置が搭載されており、そこで酸素と水素を反応させて電気を作り、その電気でモーターを駆動して走行する。
つまりFCEVの走行には、FCスタックへの酸素と水素の供給が不可欠。このうち酸素を供給する役割を担っている製品が、エアコンプレッサーである。
一方、水素は高圧水素タンクから供給されるが、発電時に一部、未反応となる水素が出てくる。その水素をFCスタックから吸引し、再びFCスタックへ送り、燃費を向上させる役割を担う製品が水素循環ポンプである。
このようにエアコンプレッサーと水素循環ポンプは、FCEVの発電システムにおいて重要な役割を担っている。どちらもガソリン車のエンジンに相当する機能を構成していると考えてもらえば分かりやすいだろう。両製品は、カーエアコン用コンプレッサーとは全く異なる機能部品だが、コンプレッサー事業部で長年培ってきた圧縮技術を活用して開発し、FCEVの商品力向上に貢献している。
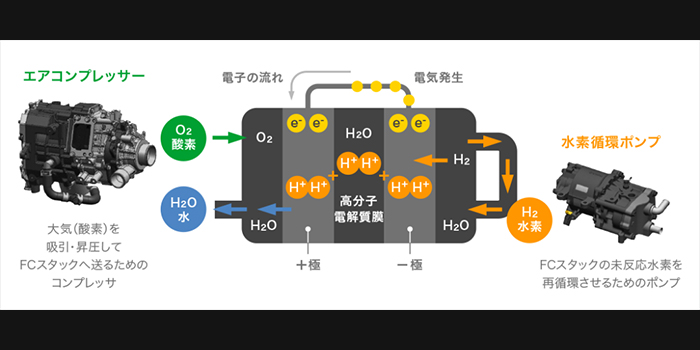
STORY 3
エアコンプレッサー開発1: 世界初の機構。
新たなエアコンプレッサー開発に当たって不可欠だったのは、初代よりも高流量・高圧力の酸素をFCスタックへ送り込めるようにすることだった。FCスタックの出力を向上させるためである。伊藤は入社して配属された後、早速この難題に挑むことになった。
「目標とする流量・圧力が数値で定められていたので『やりがいがあって面白そうだな』と感じたのが第一印象でした。配属されたばかりでハードルが高いのかどうかもよく分からなかったんです。目標数値を達成するのがいかに大変かは、その後、身に染みて感じました(笑)。でも、最先端のプロジェクトに若手がいきなり携われることは、豊田自動織機の大きな魅力の一つだと実感しています」(伊藤)
流量・圧力アップへのポイントとなった箇所が、モーターの回転数を高める「増速機」だ。今回、量産品としては世界初(※)となる「可動ローラー式増速機」を新開発した。3つのローラーで構成され、そのうち1つが空気流量の変化に対応して最適位置に自動調整される機構になっている。この機構により、市街地走行などの低速域では可動ローラーとシャフトの間の締め力が緩む。そのため、動力の損失を防ぎ、エアコンプレッサーの消費電力を大幅に低減することができ、車両の燃費向上にもつながった」
「可動ローラーの機構を成立させるのは、とても苦労しました。長時間にわたる試験を何度も繰り返し、設計にフィードバックして最適な形状を追求しました」(伊藤)
また、「さまざまな部署が協力してくれたおかげで課題を解決できたことも印象深かった」と伊藤は振り返る。
「例えばインペラーという部品を設計する際は、エンジン事業部のターボチャージャーを開発している設計者からアドバイスをもらいました。素材についても技術・開発本部に材料開発専門のグループがあるのでその部署の協力を得ました。こうして加工コスト低減とワイドレンジな運転が可能なインペラーを新たに開発することができたのです。私たちコンプレッサー事業だけでなく、豊田自動織機全体がチームワークを発揮して開発した製品だと感じています」(伊藤)
※当社調べ
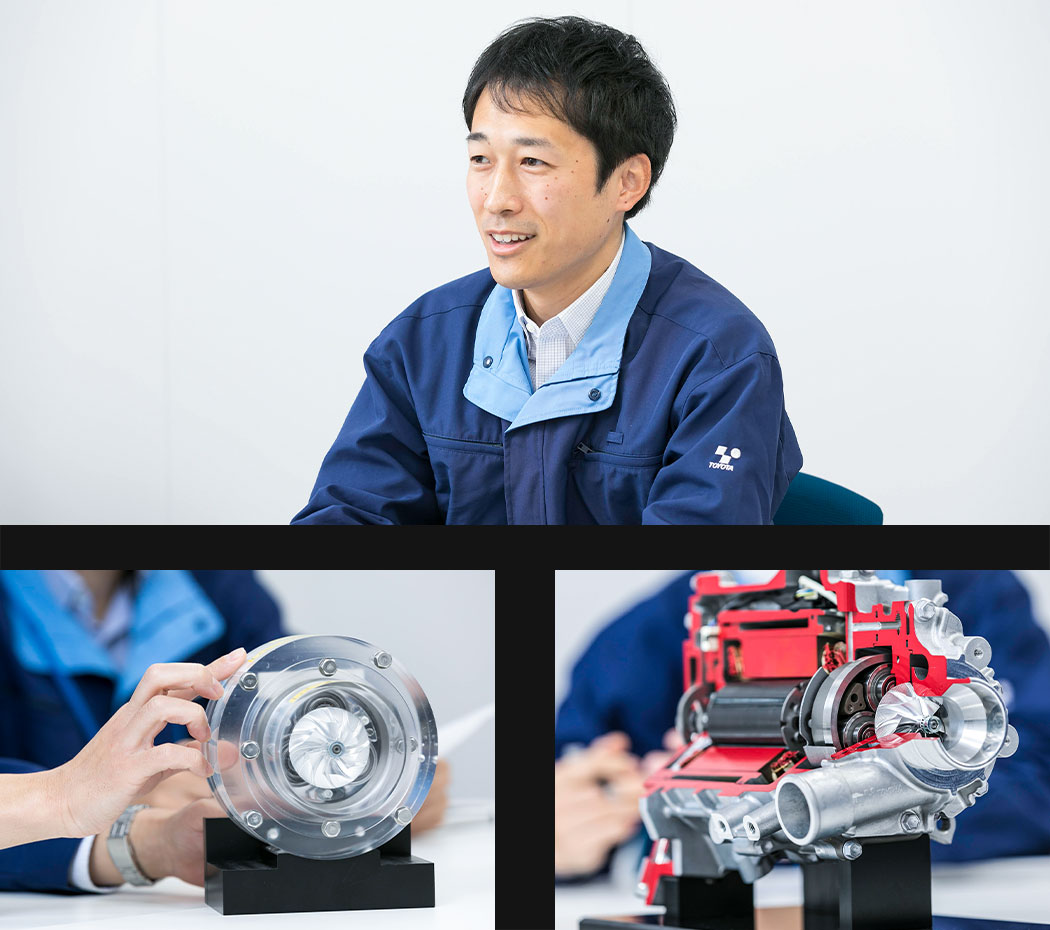
STORY 4
エアコンプレッサー開発2: 耐久性の向上。
クルマに搭載される製品にとって耐久性は極めて重要なファクターだ。高地、砂漠、雪国など、あるゆる条件において長い年数、長い距離を走ることができるか。さまざまな使われ方を想定した耐久試験をクリアしなければ、量産化のフェーズへ進むことはできない。今回開発したエアコンプレッサーについて、「いかに耐久性を向上させるか」を追求したのが高瀬だ。
「試作品による耐久試験ではさまざまな問題が起きました。問題が起きたら原因を突き止め、改善に取り組む。しかし改善効果が見えてきたと思ったら、また次の問題が現れる。原因究明と改善を同時進行で進める大変な日々でした。乗り越えられたのは、チームの力だと実感しています。織機の良いところは、配属直後の若手でもOJTを通して問題解決に携われることです。当時は分からないことばかりで覚えることが多く大変でしたが、先輩や同期の協力を得ながらやり遂げることができました」(高瀬)
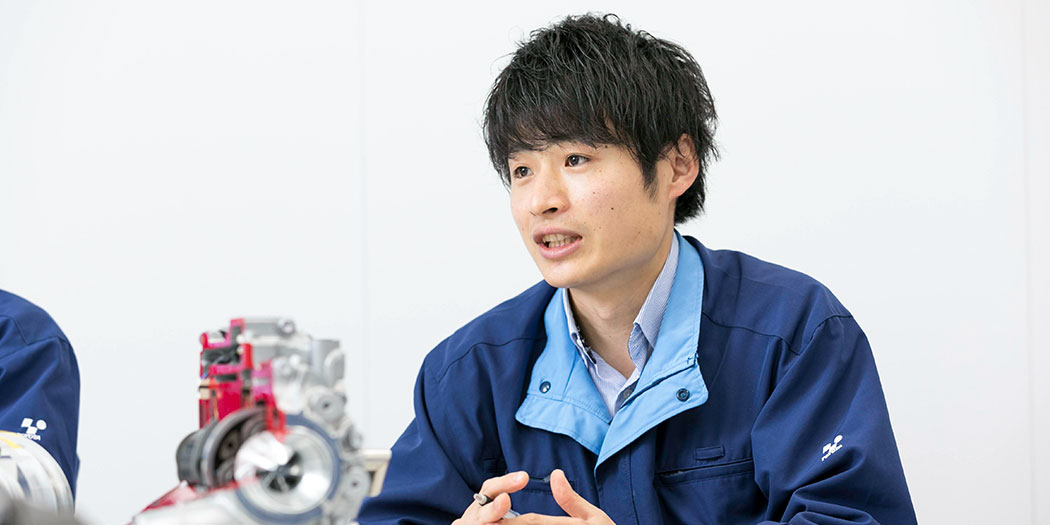
STORY 5
水素循環ポンプ開発1: より低コスト・軽量化へ。
水素循環ポンプは、開発のスタート段階で素材を従来のステンレスからアルミに変更することが決まった。低コスト・軽量化を実現するためだ。しかしその一方で、耐食性をどう確保するかが課題となった。アルミはステンレスよりも腐食しやすい。この課題の解決に取り組んだのが篠田だった。
「アルマイトコーティングという耐食性向上処理を施しても、それだけでは信頼性を確保できるまでには致らず、最初は苦労しました。水素循環ポンプの搭載位置が、初代よりも厳しい環境になったんです。初代では周囲をガードされていたのですが、第2世代ではタイヤに近く、水もどんどんかかるような位置になりました」(篠田)
なぜそのような位置に変わったのか。背景にはFCEVの普及を目指すトヨタ自動車の戦略があると伊藤は解説する。
「初代のMIRAIは専用のプラットフォームを使用していました。FCスタックの搭載位置は初代ではフロア下でしたが、第2世代はいわゆるエンジンルーム内に変更されています。トヨタ自動車はいろいろな車種への展開を考慮してFCシステム全体をつくっているんです。全体の最適化を進めた結果、水素循環ポンプの搭載位置は厳しい環境になりました。でも、それによって車種展開の可能性が広がり、FCEVの普及により貢献できるのです」(伊藤)
篠田は課題の解決策として、新たなシール構造を開発した。
「シールとは、身近なもので言えば水道のパッキンのようなものです。水素を漏らさないようにする、オイルを外に出さないようにする、外からの水を中に入れないようにする、という3つの役割が主にあります。大きなシールにすれば課題は簡単にクリアできるのですが、小型化に貢献するためにできる限り小さな構造にしながら役割を果たせるシールにすることにこだわり、形状をつくっていきました」(篠田)
最適な形状を見つけるために特に力を注いだのが、わざと腐食させた試作品の観察だった。
「ボルトを外せなくなるほど朽ち果てた試作品をハンマーで叩いて分解し、どこがどのように腐食しているかをつぶさに観察しました。中を見るのは大変でしたが、そこにいろいろなヒントが詰まってるんです。誰よりも細かく観察した自信があります」(篠田)
その観察が「新シール構造」の誕生につながった。H形の構造に押付突起が付いたものだ。その高い気密性が、アルミ製水素循環ポンプの成立に大きな役割を果たしている。
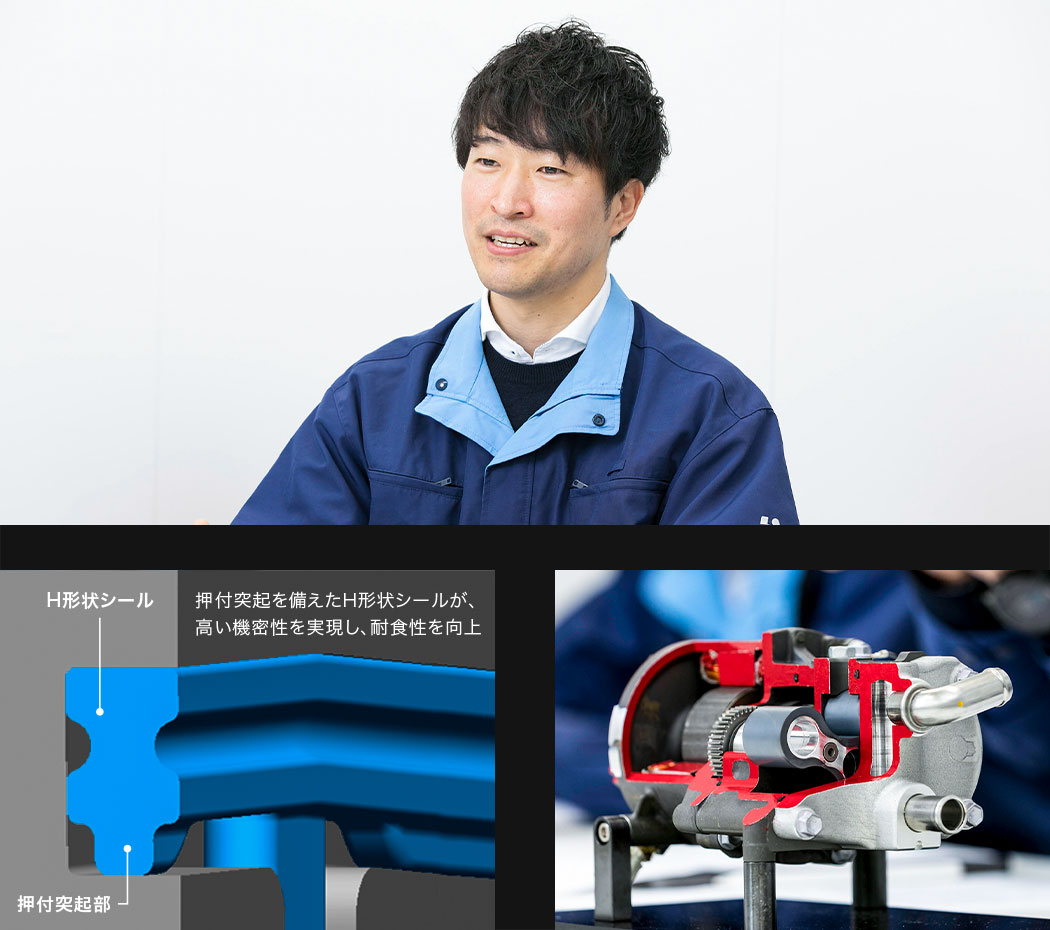
STORY 6
水素循環ポンプ開発2: 新機構の設計。
アルミはステンレスと比較して温度上昇によって膨張しやすいため、いかに温度上昇を抑制するかも課題となった。水素循環ポンプの設計・評価を担当した高荷は、試行錯誤の末、「キャッチタンク」と呼ばれる新機構を設計した。
「ギヤ室の中は通常、オイルで満たされています。オイルはギヤで撹拌されると熱を持ってしまいますが、かと言って、ある程度のオイルを入れなければ、車両停止中に必要な箇所にオイルが行き渡りません。そこでオイルの逃げ道となる『キャッチタンク』をつくったんです。これによって運転中は液面が下がってあまり撹拌抵抗が生まれず、かつ、停止中のオイル量を維持できるようになりました」(高荷)
開発の過程では、中を見ることのできるポンプをアクリルでつくり、オイルが狙い通りに行き渡るかどうかを確認した。
「やはり現物で確かめないと分からないことはあります。もしオイルが狙い通りに行き渡らなかったら水素循環ポンプの寿命に影響しますから、念入りに確認しました。可視化して、確かめて、改善する。このサイクルを繰り返して、今の形状にたどり着いたんです」(高荷)
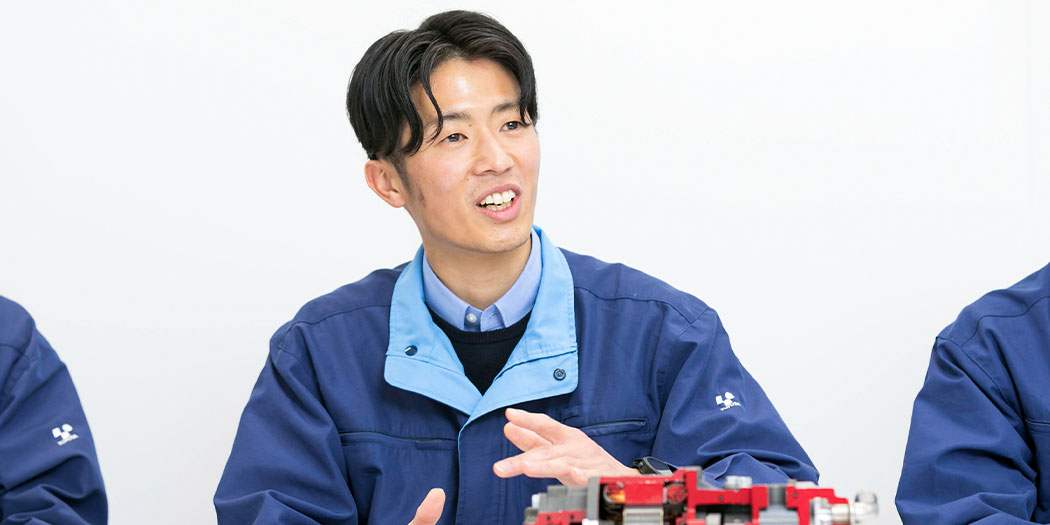
STORY 7
低NVの追求: FCEVならではの難題。
低NV(Noise:騒音とVibration:振動)の追求も、FCEV製品の開発において重要なテーマだ。
「FCEVはエンジンの音・振動がない分、各部品の音と振動に対する要求水準が非常に高いんです。特に私たちのつくるエアコンプレッサーと水素循環ポンプは特に難しい部類に入ると思います。それはクルマが走っていないときも動き続けている製品だから。電力を供給するための製品なので、例えば赤信号での停止時も動き続けている必要があります。そのとき、駆動用のモーターは動いていません。つまり他に音を発するものが何もない。そのようなシーンでも音や振動が気にならない製品にする必要があるんです」(伊藤)
エアコンプレッサーのNV性能を担当したのが渡辺だ。
「気になる音が聞こえたときに、まず音の原因を突き止めるのが難しかったですね。音の周波数を解析し、モーターの回転などと照合してどの部品が該当するかを特定していくんです。でも、部品単体では問題がないのに実際に組むと問題が出ることもあったり、一つ一つ原因を見つけてつぶしていくのにとても苦労しました」(渡辺)
水素循環ポンプについても、トヨタ自動車での車両評価において不規則異音が発生し、対策を求められたことがあった。
「カチャカチャ、という音が運転中に聞こえるという指摘をいただいたんです。難しいのは常に聞こえるわけではなく、ある条件下になると聞こえること。構成する部品を一つずつ取り外して回したり、高速度カメラで回転体の挙動を可視化するなどして、原因の究明に取り組みました。その結果、スプライン結合部という箇所で不規則異音が発生することを突き止め、対策を施すことができたんです」(高荷)
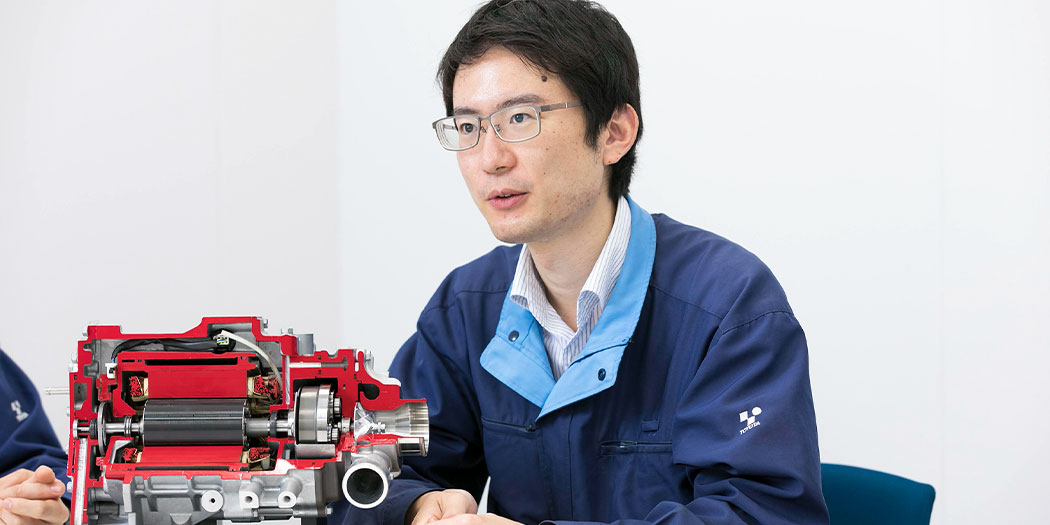
STORY 8
エンジニアたちの探究心とともに、未来へ。
高効率化、小型・軽量化、NVなど、あらゆる角度から課題解決に取り組み、第2世代MIRAI向けのエアコンプレッサーと水素循環ポンプは完成した。その過程で積み重ねた試行錯誤と改善は、メンバーたちを大きく成長させた。
「開発当初から携わったので、製品の検討から解析、部品の作図・手配、それらの評価・分析、さらにお客さまに報告する資料作りまで、一通り経験することができました。こうした幅広い経験を積むことができる、マルチプレイヤーが生まれやすい環境も豊田自動織機の魅力の一つだと思います。個人的には特に、大人数の中で各担当に配慮しながら仕事を進めるスキルが伸びたと感じています。今後もそのスキルを生かしていくと同時に、大人数の中で自分が変革者となり、周囲に影響を与えて物事をより良く変えていけるようになっていきたいと考えています」(伊藤)
「私も設計・評価をはじめ、幅広く経験できたことが一番の収穫だと感じています。特に生産技術部門のエンジニアや製造現場で作業する皆さんとやりとりできたことは、とても有意義な経験でした。『こういう設計だと組み立てやすい』という声を直接聞くことができたので、次の設計に生かしていきたいですね」(高荷)
「お客さまが求める課題解決策をいかに早く出すかを意識し、製品の耐久性評価に取り組んできました。今後はそこから一歩進んで、自分から『このような課題解決策をお客さまは求めている』と考え、提供していきたい。それを実践できるポテンシャルを培うことのできたプロジェクトでした」(高瀬)
「今はエアコンプレッサーのNVを担当していますが、一時期は水素循環ポンプのNVに携わっていた時期もありました。両方のNVを経験したことで、視野が広がったと思います。今回のプロジェクトを通じて習得した技術・知識を生かして、今後もさまざまな製品で騒音・振動の課題を解決していきたいと考えています」(渡辺)
「私もさまざまな製品を設計できるエンジニアになることを目指していきます。その一環で、現在は水素循環ポンプのチームからエアコンプレッサーのチームに移り、次のプロジェクトを進めています。社内にはさまざまな分野のスペシャリストがいるので、そういった方々と連携して多くの知識・技術を吸収しながら一人前の技術者になっていきたいと考えています」(篠田)
若きメンバーたちが培った知見、そして「最先端領域の難題に立ち向かい、やり遂げた」という自信は、新たなプロジェクトの中で発揮されている。第3世代のFCシステムへ。さらなる原価低減へ。商用車展開に向けた長寿命化設計へ。絶えることのないエンジニアたちの探究心とともに、豊田自動織機はこれからも製品の性能向上を通じてFCEVの普及・拡大に積極的に取り組み、水素社会実現に貢献していく。
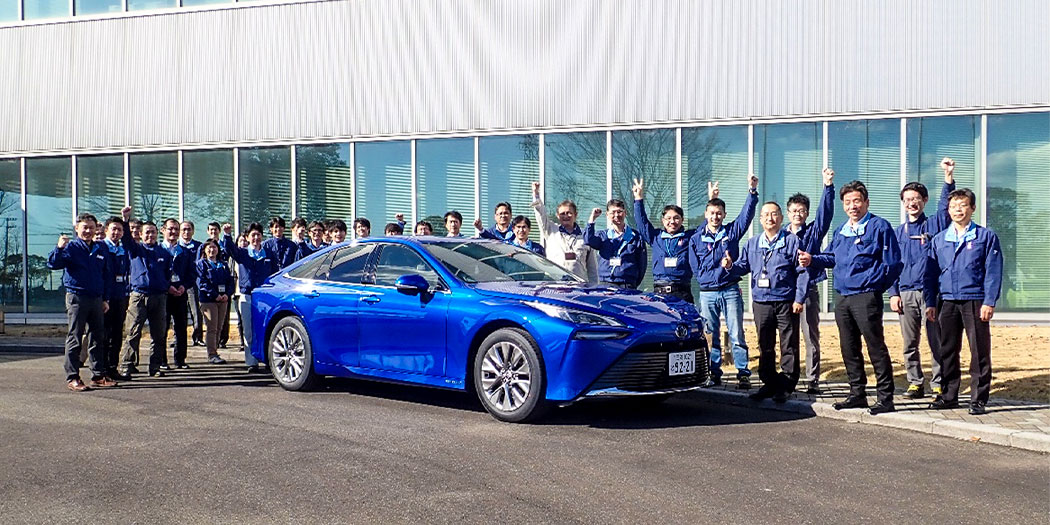