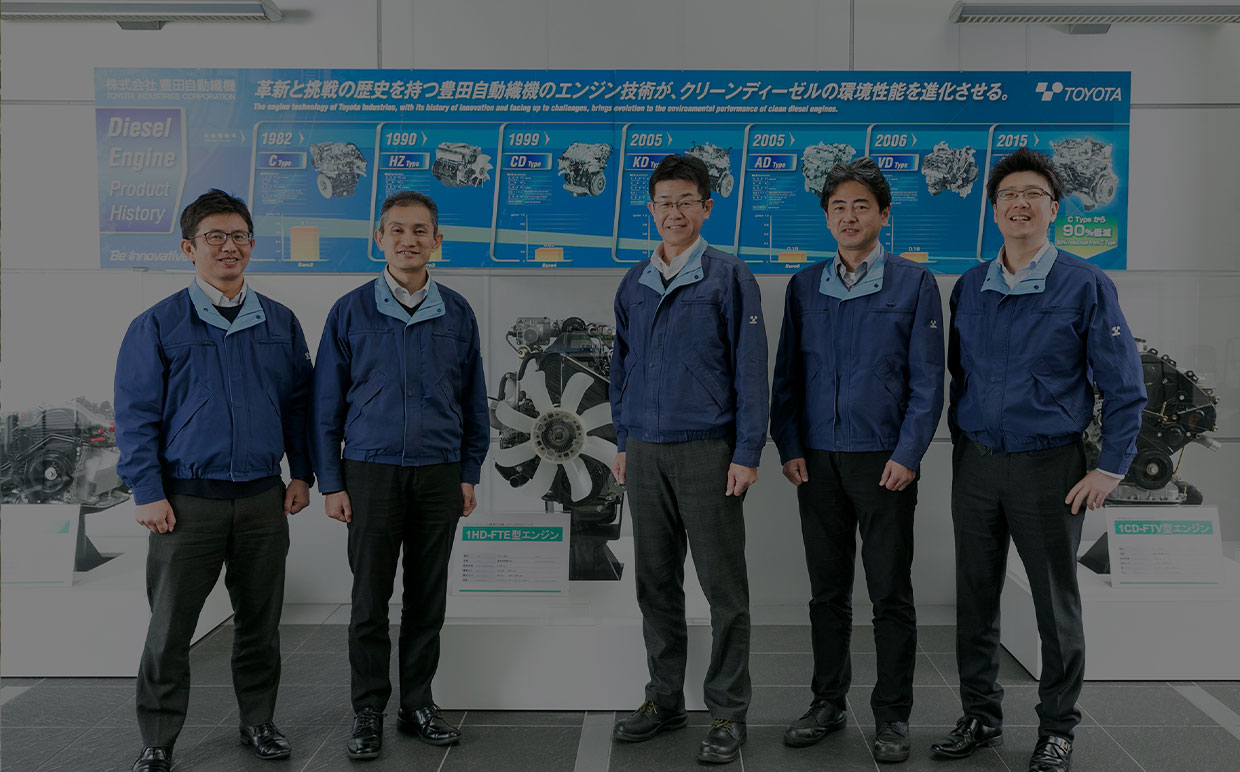
エンジン
新型ディーゼルエンジン
2拠点同時生産準備
チームで乗り越えた壁。
挑戦が壊した壁。
MEMBER
-
エンジン事業部
生産技術部
林 健一郎 -
エンジン事業部
生産技術部
北村 克彦 -
エンジン事業部
生産技術部
松浦 秀幸 -
エンジン事業部
生産技術部
近藤 博文 -
エンジン事業部
生産技術部
大竹 直也
STORY 1
生産準備とは、何を行うのか。
「日本とインドの生産準備を同時に?」―プロジェクトの概要を聞いた瞬間、生産技術エンジニアの北村は「経験したことのない壁を乗り越えなければならない仕事になる」と腹をくくった。
世界各地を走るトヨタ車に搭載されている、豊田自動織機のディーゼルエンジン。その事業の強みは、企画・開発から生産まで、一貫体制を敷く点にある。今回のプロジェクトストーリーでスポットを当てるのは、その開発と生産の間にある「生産準備」というプロセスだ。
生産準備―あまり馴染みのないプロセスかもしれない。もちろん、言葉から想像することはできる。生産への準備を行うプロセスだ。しかしその内容は皆さんの想像をきっと超えている。
開発部門がどんなに優れた製品を開発しても、生産ラインで造ることができなければ意味はない。生産技術エンジニアは開発のフェーズにも参画し、どうすれば造りやすくなるか、試験も含めた活動をする。そしてここからがメインの業務。製品をどのような方法と順序で造ればよいかを企画・検討し、設備メーカーから設備を調達する。このフェーズでは設備メーカーに出向き、問題なく生産できるかをチェックするのも重要な仕事だ。そして最後のフェーズでは調達した設備を工場に設置し、設計通りに量産できるよう調整し、ラインオフを迎える。
これら一連の流れを担い、品質、生産効率、コストという相反する要素を同時に成立させる生産ラインを追求していくプロセスが生産準備だ。ディーゼルエンジンの場合は数年をかけて行われる。数多くの部品で構成されるため、一つのプロジェクトに必要な生産技術エンジニアの人数も多い。その一人一人が創意工夫と試行錯誤を重ねて遂行する業務なのだ。
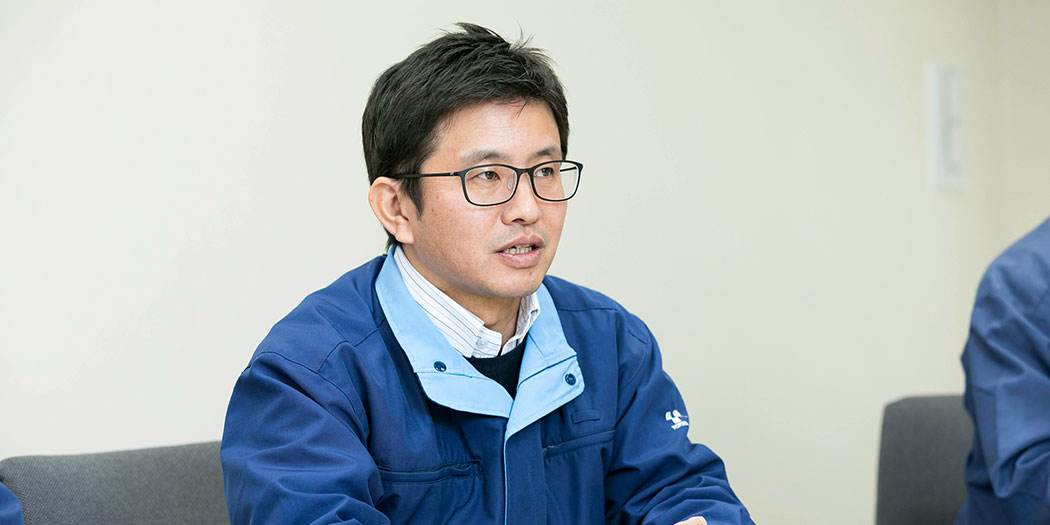
STORY 2
「生産準備のための準備」を徹底。
2拠点で同時に生産準備を進めることになった製品は、トヨタ自動車の新興国世界戦略車IMV(Innovative International Multipurpose Vehicle)シリーズに搭載される新型ディーゼルエンジンだ。IMVの販売が好調なため、生産能力を当初の予定よりも増強することになり、その新たな生産拠点として国内の東知多工場とインド現地法人の工場が選定された。
2拠点で同時に生産準備を進める場合、通常であれば2つの生産準備チームが組まれる。しかし当時の社内は2チーム分の人員を確保できる状況になかった。では、どうするか。プロジェクトを立ち上げた林の答えは明快だった。
「1チーム分の人員で、2拠点の生産準備に取り組む計画を立てました」(林)
そうするしかない。しかしもちろん、全メンバーが同時に倍の仕事をこなすことを前提とした無謀な計画を立てたわけではない。共通化できるものを徹底的に共通化するなど効率を高めることが成功の鍵を握ると考え、まず周到な事前検討から始めた。製造部門や品質管理部門などの他部署も巻き込み、いわば「生産準備のための準備」を徹底したのだ。
「仕様書の作成段階で、設備を内製している部署である生技開発センターのエンジニアにも参加してもらいました。合言葉は『やり直しレスの生準』。後の工程でやり直しが出ないよう、設計する前に設備の作り手の視点からアドバイスをもらうことにしたのです」(林)
シリンダーヘッド、シリンダーブロックなどの部品のワーキングリーダーを務めた北村は「まず、どのような考え方でみんなをリードしていくかを検討しました」と振り返る。
「両拠点の加工ラインについて、共通にする設備と変える設備を一覧にするなど、考え方の整理から入りました。最初にメンバー間で共通認識を持つことを重視したのです」(北村)
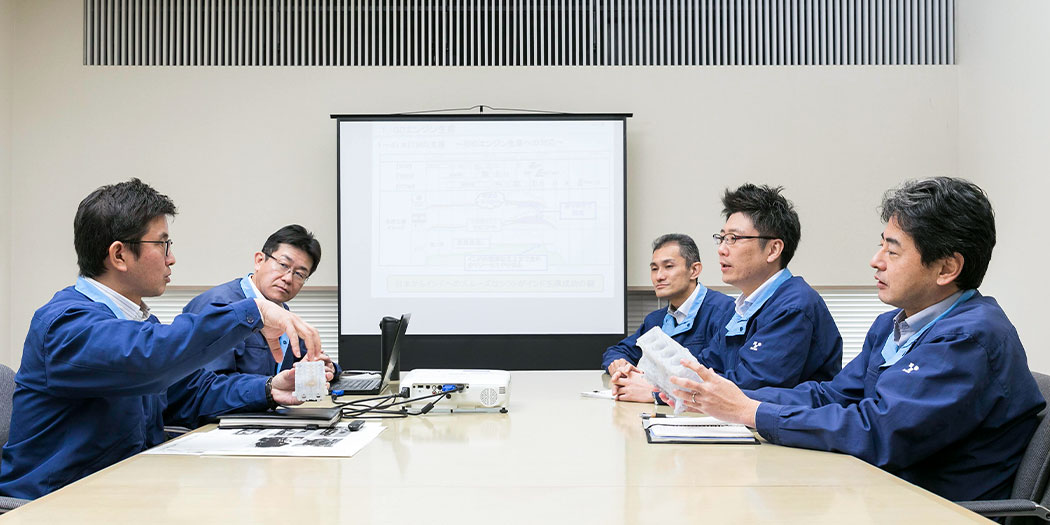
STORY 3
「現地調達化の拡大」という難関。
このプロジェクトには「少人数」の他にもう一つ、大きな課題があった。それは「いかに投資を抑えるか」だ。製品としての競争力を確保するために、避けては通れない課題だ。
この課題の解決に向けて、東知多工場の生産準備は「既存設備をオーバーホールして活用することで、新規設備への投資を抑える」という方針で進められた。
一方、インドの生産準備においては現地調達化の拡大に取り組んだ。海外で生産準備を行う場合、基本的に設備は日本国内の設備メーカーから購入し、それらを海外に運ぶ。今回はその数を減らし、インドの設備メーカーからの購入を増やすことでコスト抑制を目指したのだ。
この現地調達化の拡大が、今回のプロジェクトにおける最大の難関となった。
「当初は約10%の現地調達率を目指していました。比較的難度の低い工程の設備だけを、インドで購入しようと考えていたのです。しかし、それでは競争力がどうしても足りない。現地調達率をさらに上げることを目指しました」(林)
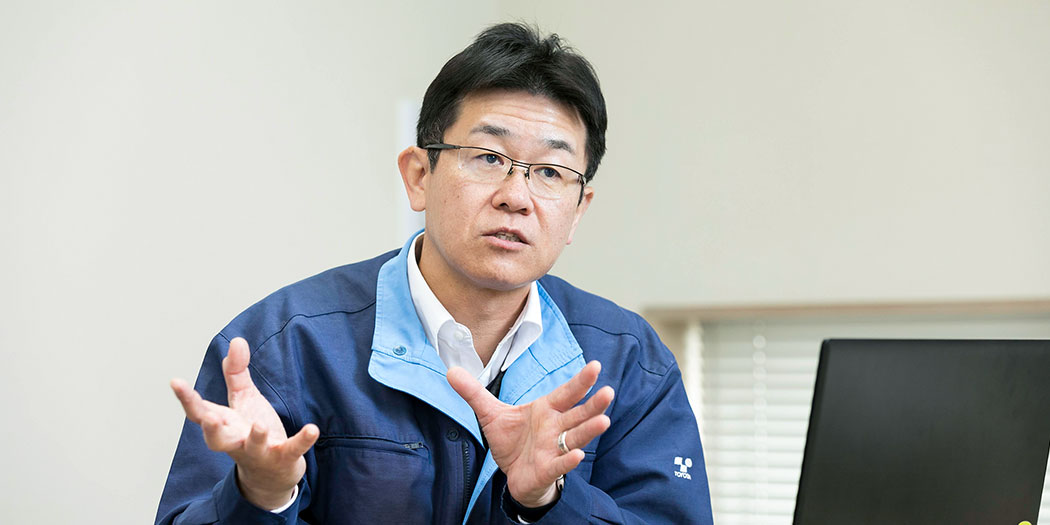
STORY 4
国内で積み重ねた経験を発揮。
現地調達設備は、基礎試験による検証を実施しながら選定が進められた。選定活動を担当した大竹は、このプロジェクトに携わる前、生技開発センターに所属していた。設備を評価するポイントは、その時にしっかりと学ぶことができた。
「まだ若手でしたが、現地調達設備の選定活動を任せてもらうことができました。特に数多くの台数を購入する予定の設備を検証する際は『失敗するわけにはいかない』という大きな責任を感じましたが、生技開発センターで学んだことを発揮して取り組みました」(大竹)
クランクシャフトなどのワーキングリーダーを務めた松浦は、設備の選定に当たって現地の設備メーカーを一件一件回った。海外拠点の生産準備は自身にとって初めて。しかし、クランクシャフトの生産準備については、国内で経験を重ねた自負と誇りを持っていた。
「これまで積み上げてきたものを全て発揮する集大成のつもりで、このプロジェクトに臨みました。現地メーカーの設備が実際に使えるかどうかは、造っている製品や工場の様子を自分の目で確かめないと、やはり判断できません。工程に必要な設備の種類も多いので視察するメーカーも多く、日本とインドを行ったり来たりしていました」(松浦)
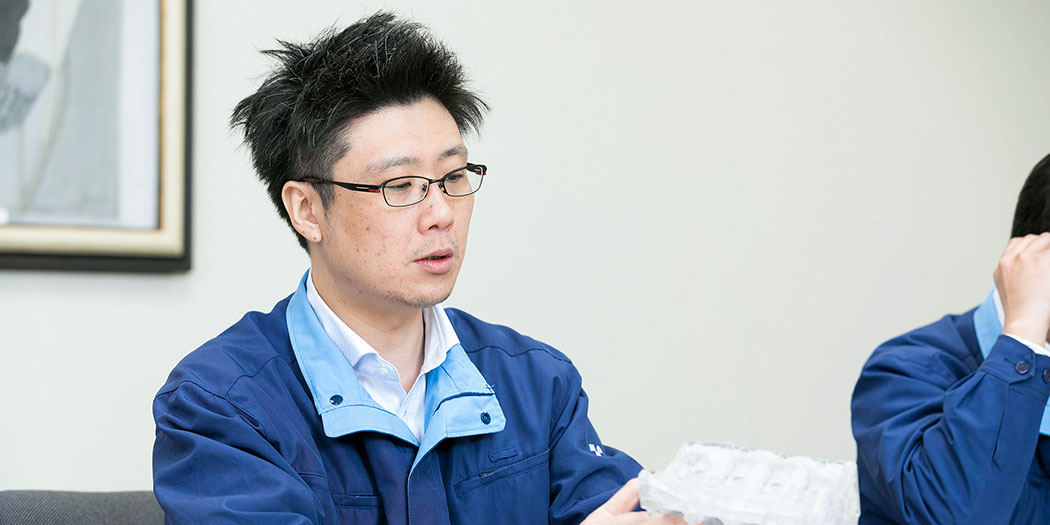
STORY 5
通用しない「あうんの呼吸」。
メンバーたちは、品質、生産効率、コストを成立させるために労を惜しまずに動き、設備メーカーを選定した。そして各社へ仕様を提示し、いよいよ設備製作へ。しかし、このフェーズで現地調達の難しさをさらに痛感することになる。
「日本の設備メーカーと私たちの間には、いわば『あうんの呼吸』があるんです。私たちの提示した仕様を見て設備メーカーは『こういう設備にしたいんですね』と読み取ってくれる。きっちりと図面にして、実際の形にしてくれる。しかし、インドではそうはいきません。『あうんの呼吸』は通じないのです。ゼロから全て細かく伝えないと、目指す設備に近づいていかない。そのような経験はなかったので最初は戸惑いました。何度もやりとりを重ねながら、お互いの間にあるギャップを埋めていきました」(松浦)
組付ラインのワーキングリーダーを務めた近藤も、現地調達ならではの難しさを感じていた。
「組付ラインでは、トヨタのインド工場で採用された設備を製造している現地メーカーを選定しました。その実績があるので、設備製作のフェーズに入る前は安心していたんです。もちろん選定時には実際にそのメーカーを訪問し、確認もしました。造っている設備に何の問題もありませんでした。ところが今思えば、その時点で問題がないのは当然なんです。完成した設備をトヨタが採用しているわけですから。完成に至るまでに長い道のりがあったことに私は気付いていなかった。数多くのトライ&エラーを重ねて完成したのがあの設備だったんだ――後に、私自身がトライ&エラーを重ねる中で、そう気付きました」(近藤)
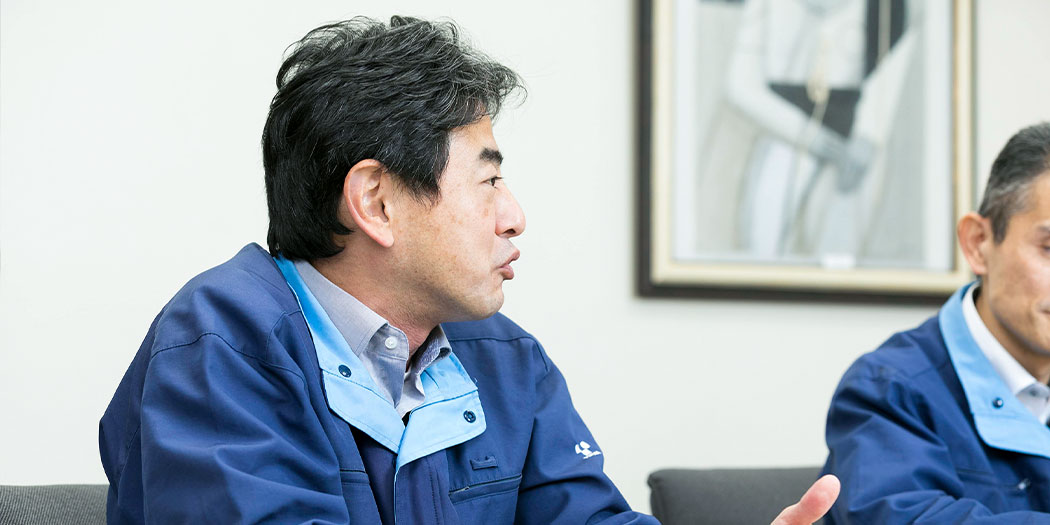
STORY 6
ピンチを救った豊田自動織機の風土。
時間やビジネスに対する感覚の違いもメンバーたちを悩ませた。インドに駐在し、現地メーカー各社の日程管理を行っていた大竹は「予定通りの日程で設備が仕上がらないケースは多々ありました」と振り返る。
「このままではラインオフに間に合いません、と日本側に助けを求めた設備もありました。すると生技開発センターのエンジニアを、急きょインドに派遣してくれることになったんです」(大竹)
大竹は早速、生技開発センターのエンジニアと共に設備メーカーへ向かった。エンジニアは製作途中の設備を見て、がく然としていたという。
「計画よりも大幅に遅れている上、組み付けた部品も図面通りになっていない。そのような状態から、生技開発センターの皆さんは設備を仕上げてくれたんです。目標に向けてみんなで力を合わせる豊田自動織機の風土を、これほどありがたいと感じたことはありませんでした」(大竹)
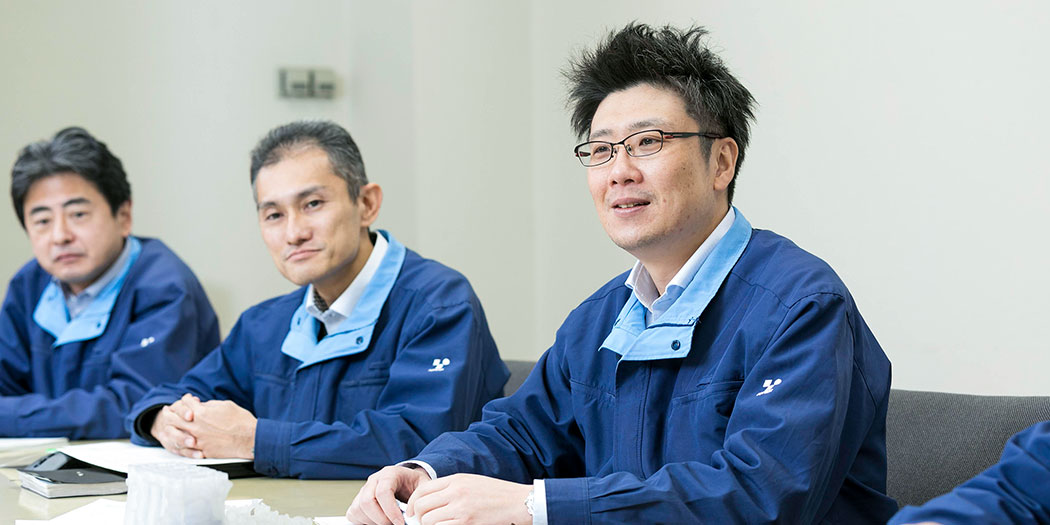
STORY 7
困難があったから、技術を深掘りできた。
周到に事前準備をしたが、それでもいくつもの予期せぬ壁が立ちふさがった。それらの壁をメンバーたちは一つ一つ乗り越えた。当初約10%が目標だった現地調達率は約40%を達成し、製品としての競争力向上に大きく貢献。そして最後には予定通りにラインオフを迎えることができた。
特に現地調達化を拡大する取り組みには大きな困難が伴ったが、その分、メンバーに大きな収穫をもたらした。
「現地メーカーの皆さんにきめ細かく指示するために、これまで設備メーカーに任せていた領域も自分で調べる必要がありました。大変でしたが、そのおかげでさまざまな技術を深掘りできたんです。例えば鋼材を加熱して硬くする『焼き入れ』という工程の設備については、温度や時間の条件設定にまで踏み込んで調べ、技術を自分のものにできました。この経験を経て、新規エンジンの設計に携わる際、設計者が要求する内容に対して自身の対応の幅が広がったと感じています。」(松浦)
「毎日のように設備メーカーを回る中で、設備が完成するまでの過程をしっかりと覚えられたことが、私にとって大きな財産となっています。図面を見てどのような設備が完成するか、イメージが湧くようになりました。また、図面を使って定量的に意思を伝え合うスキルが身につき、それは帰国後、経験の浅い若手エンジニアとのやりとりにも生きました」(大竹)
STORY 8
「受け入れる」というより、「受け入れてくれた」。
メンバーの心の中にある「多様性」に対する価値観にも変化が起きた。多様性について語るとき、一般的に「受け入れる」という言葉がよく使われる。しかし、メンバーが現地でインド人とのコミュニケーションを重ねる中で芽生えた価値観は、それとは少し違った。
「私たちがインドの皆さんを『受け入れる』というより、インドの皆さんが私たちを『受け入れてくれた』という印象ですね。受け入れる、という表現は、ちょっと自分中心のニュアンスを感じてしまう。自分の価値観や考え方を『当たり前』だと思ってはいけない。その大切さに気付きました。これは日本人同士でも同じことだと思います」(大竹)
「確かにそうですね。受け入れてもらったのは私たちです。現地の皆さんは、私たちが真剣に、必死に取り組んでいる姿を見て、ついてきてくれたと感じています。私は英語はあまりできない方だけど、意外と何とかなりました(笑)。一生懸命さは言葉がなくても伝わるものです」(松浦)
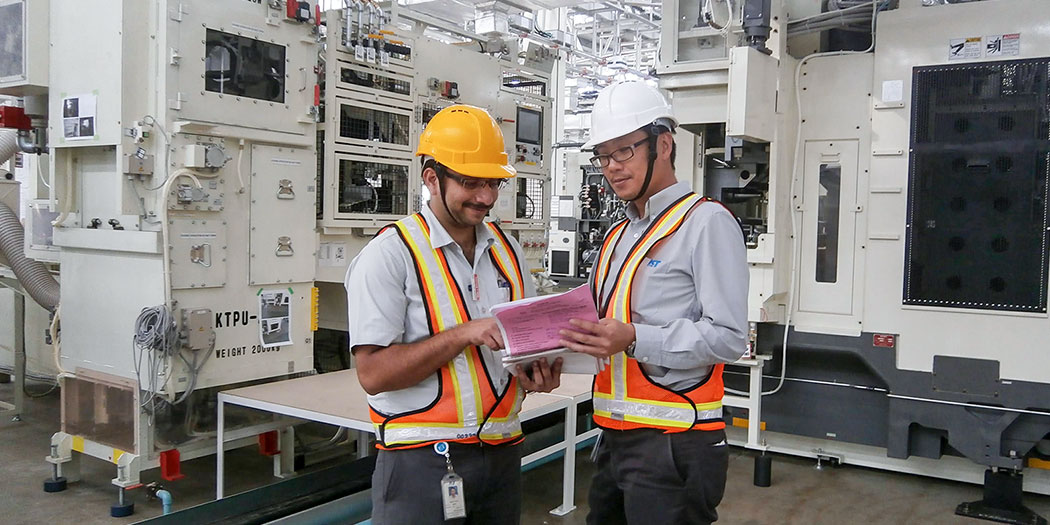
STORY 9
チームワークの大切さを実感。
このプロジェクトを通じてメンバーが得たものは、まだ他にもある。それは一番大きなものかもしれない。チームワークの大切さを実感したことだ。
「海外の生産準備では、日本で仕事をしているときよりも、設備メーカーの皆さんや製造部門の人たちと強い絆ができるんです。日々の仕事の中身は濃いですし、毎晩一緒に食事もするので、本当の意味の仲間になるんですね。すると帰国してからも、そのつながりがあるので、次の仕事がとてもスムーズに進められるんです。今回のプロジェクトメンバーも今、インドで培った人脈をフル活用していると思います」(林)
「まさしく今、インドの生産準備で培ったつながりをフル活用しています。このプロジェクトの後に日本でラインをつくったのですが、その際、インドで一緒だった製造部門のメンバーもいました。『あの時はこうだったよね』『今回はこうしたいね』と思いを一つにしやすかったので仕様段階の完成度が非常に高くなり、やり直しのない生産準備を実践することができました」(大竹)
「今日はインドの話が中心となりましたが、実は日本においてもオーバーホールした既存設備が要求品質をなかなか確保できないなど、さまざまな問題が起きていたんです。インドと日本、双方から課題が上がってくる中で人員の配分を考えながらプロジェクトを前に進めていくのがとても大変でした。それでも2拠点同時生産準備をやり遂げることができた。この成果は組織全体に『苦しい場面もチームワークを発揮すれば乗り越えられるんだ』という自信をもたらしたと実感しています」(北村)
「インドの生産ラインを苦労して立ち上げる中で、現地の生産技術スタッフと信頼関係を築くことができたと実感しています。今は日本での生産準備を担当していますが、また機会があれば一緒に仕事をしたいですね」(近藤)
「海外の生産準備では国内のケースと比較して設備メーカーの皆さんに頼れないシーンが多いので、『自分たちでやるしかないんだ』という覚悟がメンバー間に生まれます。その覚悟のもとにチームが一つになることを実感しました。今はインドにおける次期プロジェクトを担当しています。若手メンバーが中心なので、学んできたことをしっかりと伝えていくとともに、若手が自分で成長をつかみ取るよう促していきたいですね。そうすることが豊田自動織機の生産技術全体のレベルアップにつながると考えています」(松浦)
メンバーが一つになり、いくつもの壁を乗り越えた今回のプロジェクト。それは、いくつもの壁を壊したプロジェクトでもあった。部署間の壁。考え方や価値観の壁。さまざまな古い壁を壊したことが、2拠点同時生産準備という難題を成功へと導いたのだ。
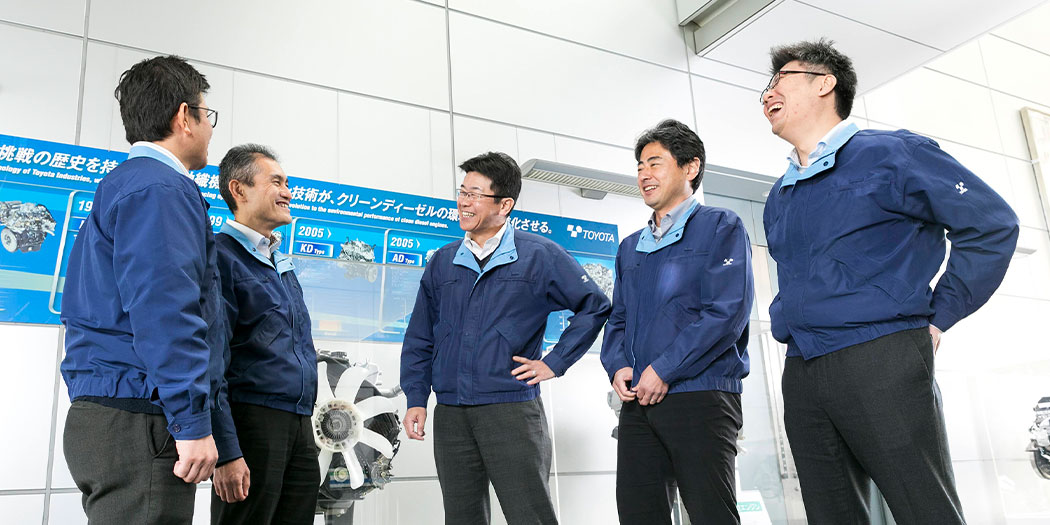