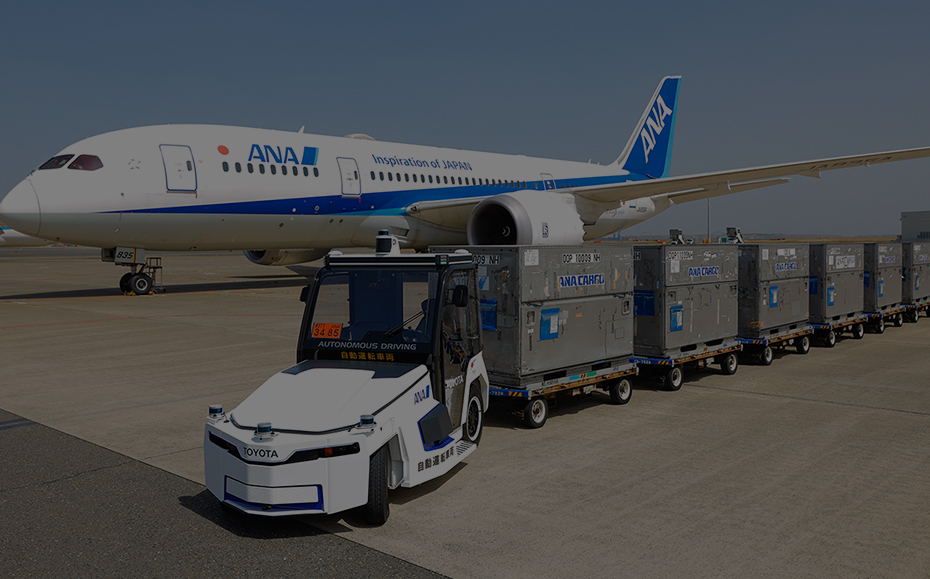
物流ソリューション
「手荷物積み付けロボット」と「自動運転トーイングトラクター」の開発
官民一体で進める
航空イノベーションへの貢献。
MEMBER
-
トヨタL&Fカンパニー
AR開発部
渋谷 修 -
トヨタL&Fカンパニー
AR開発部
望月 賢二 -
トヨタL&Fカンパニー
AR開発部
山田 彩加 -
トヨタL&Fカンパニー
製品企画部
鈴木 航大 -
トヨタL&Fカンパニー
物流ソリューション事業室
古橋 正得
STORY 1
空港を舞台にしたソリューション
豊田自動織機は、業種カテゴリーで分ければ機械メーカーに当たる。しかし、機械というモノだけを社会に提供しているわけではない。常に目指しているのは「世界の産業・社会基盤を支え、住みよい地球と豊かな生活、そして温かい社会づくり」(2030年ビジョンより)に貢献すること。そのために力を注いでいるのが、ソリューションの提供だ。社会のさまざまな分野でお客さまの課題解決に貢献することを目指し、技術を磨き、新たな価値の創造に挑戦し続けている。
物流分野で特定のお客さまにソリューションを提供した事例として、以前「ファンダランデ社製クロスベルトソーターの日本初導入」のプロジェクトストーリーを紹介した。この取り組みを「陸の物流ソリューション」と呼ぶならば、今回紹介するプロジェクトは空港を舞台にした「空の物流ソリューション」である。
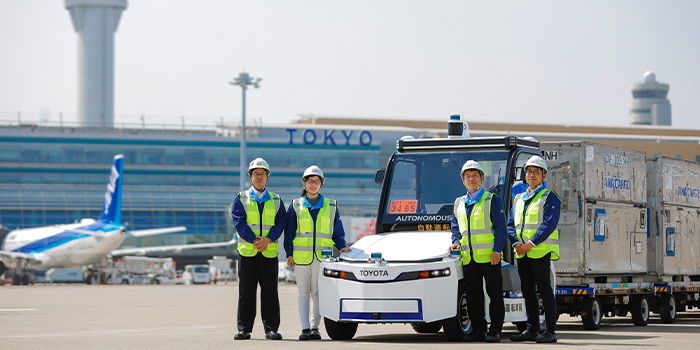
STORY 2
地上支援業務の省力化・省人化が強く求められている
空港で手荷物を預けて航空機に乗ると、目的地の空港に到着後、受け取ることができる。この仕組みをどのような物流システムが支えているか、ご存じだろうか。
その中における「手荷物が航空機に積み込まれるまで」の一般的なプロセスを簡単に説明しよう。
1 手荷物処理システム(バゲージハンドリングシステム、以下、BHS)
チェックインカウンターで預かった手荷物をベルトコンベヤーで搬送。タグの情報を自動で識別し、フライト別に仕分け、荷さばき場に運ぶ。
↓
2 コンテナへの積み込み
荷さばき場で人の手により、手荷物が航空機搭載用コンテナに積み込まれる。
↓
3 コンテナのけん引
コンテナを載せた「ドーリー」と呼ばれる台車をトーイングトラクターでけん引し、航空機直下まで運ぶ。
↓
4 航空機への積み込み
航空機の荷室にコンテナを積み込む。
手荷物カウンターで預けた荷物は、このような流れで航空機に積み込まれる。これらのプロセスにおいて課題となっているのが、労働力不足だ。生産年齢人口が減少する中で、上記プロセスをはじめとするさまざまな地上支援業務の省力化・省人化が強く求められている。そのため国土交通省航空局では「官民ロードマップ」を作成し、民間企業と連携して航空イノベーションを推進。その中で豊田自動織機は全日本空輸株式会社(以下、ANA)と共同で、上記の「1 手荷物処理システム」から「3 コンテナのけん引」までを省力化・省人化するためのプロジェクトをスタートさせた。
豊田自動織機の連結子会社であるファンダランデ社はBHSに強みを持つ。「手荷物積み付けロボット」を開発してBHSに接続し、さらに「自動運転トーイングトラクター」による無人搬送を接続すれば、手荷物を航空機に搭載する一連のプロセスを一貫して自動化できる。これは豊田自動織機だからこそ提供できるソリューションへの挑戦だ。
STORY 3
手荷物積み付けロボットの開発
手荷物積み付けロボットの開発チームはまず、課題の洗い出しに取り組んだ。自分たちの手でスーツケースの積み付けも経験した。その中で、単に自動で積み込めるようにするだけでは解決しない課題の存在に気付く。
「荷崩れが発生するのです」と語るのは、手荷物積み付けロボット全般の開発を担当する古橋だ。
「スーツケースは形も大きさもバラバラです。ランダムに流れてくるスーツケースを自動で順に積み付けていく方式では、隙間が多くなり、積載効率が良くありません。しかも荷崩れが起きやすくなることが分かりました」(古橋)
では、どのように積めば荷崩れを抑制できるのか。さらに検討を重ねた結果、サイズごとに積み付けエリアを区分けして積み付ける方法が有効であることが分かった。そして試行錯誤の末、「2コンテナ同時積み付けロジック」という独自の方法を生み出す。
「まず3Dスキャンでスーツケースのサイズを読み取り、『大』『中』『小』に分けます。そして『大』は前コンテナの奥から順に、『中』は後コンテナの奥から順に、など、サイズに応じて2つのコンテナの決められた場所に積み付けていくことで、少ない隙間で積み付けられるようにしました」(古橋)
さらに、2段目以降の高さをできるだけ揃えるアルゴリズムも取り入れた。
「どれとどれを重ねると高さの差が最小値になるかを計算して積み付け、マッチングしないものは上部に仮置きし、タイミングが整ったら積み込む。このようなアルゴリズムも構築しました」(古橋)
こうして荷崩れしにくく、手荷物の流れを止めない自動積み付けを実現。その他にも「スーツケースを回転させて、ハンドル方向を全て手前に統一して積み付ける」「ハード・ソフト両方のスーツケースを縦・横どちらの向きでも積み付けできるロボットハンド」「2Dカメラによる荷崩れ検知」など、さまざまな技術を導入。実験と評価を通じて、それぞれの完成度を高めていった。
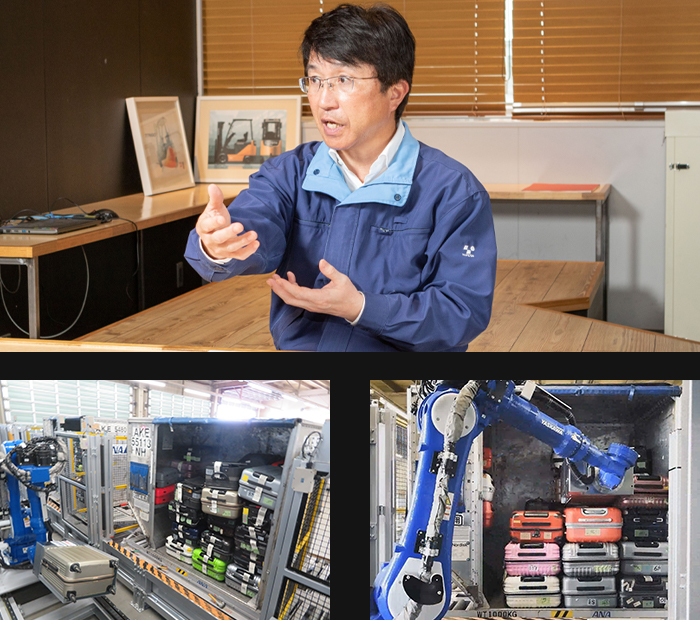
STORY 4
自動運転トーイングトラクターの開発
自動運転トーイングトラクターの開発チームを悩ませたのは「自己位置推定」の精度だ。そこには、トーイングトラクター特有の難しさがあった。
自己位置推定とは読んで字のごとく、車両に「自分が今、どこにいるかを推定」させる技術のこと。自動運転システムの鍵を握る技術であり、さまざまなものがある。自動運転化技術を担当した望月はこう解説する。
「例えば磁気誘導線を地面に埋め込む方法がありますが、空港の駐機エリアには安全基準があり、地面を掘って何かを埋めることができないのでこの方法は使えません。また、カーナビのように人工衛星を利用して自己位置を測位するGNSSという方法がありますが、積み付けエリアのある屋内では使えません。そのため今回は『路面パターンマッチング』という技術を採用しました」(望月)
路面パターンマッチングとは、車両底面に搭載したカメラで走行中に路面画像を撮影し、事前に作成した路面画像マップデータをマッチングすることで、車両の位置・姿勢情報を取得する技術。屋内外でも、誘導線がない道でも、自己位置を推定できるというメリットがある。しかし――。
「最初は屋内での認識率が非常に低く、3割程度しか識別できないという現象に直面しました。そこで私たちは、画像処理アルゴリズムなどソフトウェアの見直しとともにハードウェアと併せて調整すべきポイントを探っていきました。その結果、屋内での認識率も向上させることができたのです。同様に、雨の日の屋外も最初はうまくいきませんでした。路面が濡れると、画像が変わってしまうことが原因です。この課題についても画像処理のパラメーターを調整して雨の日も使えるよう性能を上げていきました」(望月)
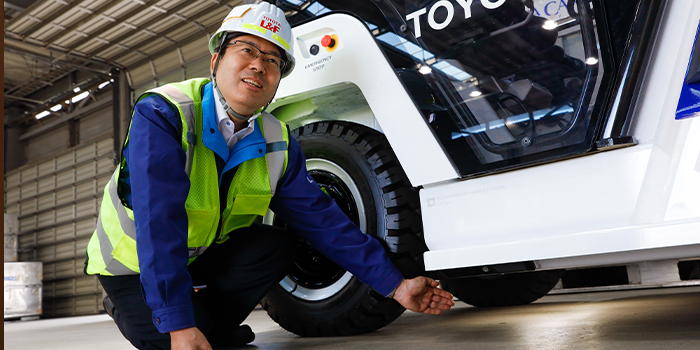
STORY 5
「接続」の課題を開発チーム間の相互理解で解決
いよいよ実際の空港でのテストへ。ANAと豊田自動織機は、手荷物積み付けロボットと自動運転トーイングトラクターを接続させた実証実験を九州佐賀国際空港(以下、佐賀空港)で実施した。
一貫した自動化を実現するための鍵を握るのは、ロボットとトーイングトラクターの接続がうまくいくかどうかだ。そのためにはトーイングトラクターを決められた位置に正確に停止させる必要がある。コンピューターで制御されているのだから正確に止まるのではないか、と思うかもしれないが、そうとは言い切れない。
「コンピューター制御でも停止位置のズレをゼロにはできません。タイヤの摩擦や積載量など、さまざまな要因でバラツキが出ます。また、トーイングトラクターは制御の下で走行させることができますが、ドーリー(コンテナを載せた台車)はけん引されているだけ。カーブの途中で止めようとするとどうしてもバラツキが大きくなるので、進入の仕方も調整しました」(望月)
ロボットとトーイングトラクターの両開発チームは緊密にコミュニケーションを図り、性能要件を理解し合い、お互いの仕様に落とし込んだ。
「車両停止精度の向上に取り組むとともに、ロボット開発チームに『許容できる“離れ量”をちょっと緩めたい』と相談しました。近過ぎるとバラツキの程度によっては接触してしまう可能性があるからです」(望月)
ロボット開発チームはその要望に応えた。
「コンテナの位置をレーザー距離測定し、どれだけ離れているか、どれだけ傾いているかを読み取り、ロボットの積み付け位置を補正するプログラムを取り入れました。これによって、ロボットとトーイングトラクターのズレに対応できる接続を実現できました」(古橋)
佐賀空港での実証実験は接続を含めて問題なく順調に進み、実用化に向けて大きく前進した。
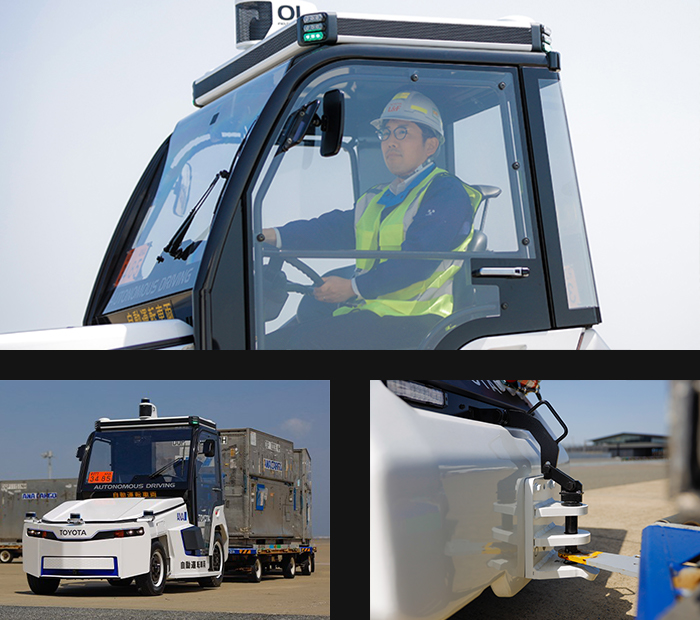
STORY 6
羽田空港での実証実験 1
手荷物積み付けロボット開発チームは、その後も継続して佐賀空港で完成度の向上に取り組んだ。
一方、自動運転トーイングトラクター開発チームはその後、中部国際空港(以下、セントレア)、そして東京国際空港(以下、羽田空港)と舞台を変えて実証実験を重ねていく。渋谷はこの過程を「ホップ、ステップ、ジャンプ」と表現した。
「羽田空港での実証実験は我々にとって、佐賀空港、セントレアでの実証実験を通じて磨いた技術の総仕上げ。ホップ、ステップという段階を経て、ついにジャンプを迎える心境でした」(渋谷)
羽田空港には総仕上げにふさわしい環境があるという。
「国内最大の空港である羽田空港は、多くの空港支援車両が混在していますし、取り扱い貨物は多く、トンネルや坂道もあります。自動運転トーイングトラクターにとって日本で最も走行条件の厳しい空港といえるでしょう。それはつまり、羽田空港で安全かつスムーズに自動走行できれば、日本中どの空港でも使えるものになるということです」(渋谷)
走行条件の厳しい羽田空港に対応できるよう、この実証実験に向けてより高度な自己位置推定性能と走行性能を兼ね備えた車両を新たに開発した。渋谷はその開発において機種リーダーを務めたが、開発に当たって何よりも重視したのは「安全」だという。
「一般の方は『空港は、公道と違って閉鎖された空間で決まった経路を走ればよいし、障害物もないから自動走行しやすいのでは?』と思うかもしれません。しかし実は、空港での自動走行は、公道よりも難度が高いのです。横断歩道のないところを人が歩いていますし、自転車や他車両も走っています。障害物を検知したときに、自動で止めるのか、自動でよけるのか、それを判断させることは難しい。安全のためには止まるのが基本です。しかし障害物の検知範囲を広くしすぎると対向車両も全て検知して停止し、他車両の運行を妨げてしまいます。このような難しい調整が空港における自動走行では必要なのです」(渋谷)
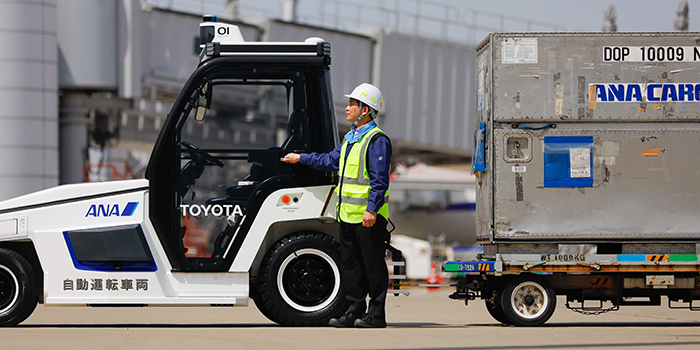
STORY 7
羽田空港での実証実験 2
羽田空港の実証実験では、新たな自己位置推定技術を取り入れた。担当した山田はこう説明する。
「路面パターンマッチングだけでなく、GNSS(人工衛星を利用した全世界測位システム)も取り入れました。自己位置推定を二重化することで、もしどちらかのセンサーに不具合が起きても、もう一つのセンサーで自動走行を継続できるようにするためです」(山田)
しかしその二重化によって課題が生じたという。
「路面パターンマッチングとGNSSの座標系が異なるので、2つの座標系を合わせこむことに苦労しました。最終的には他の部署の方や先輩にも協力してもらい、解決することができました。ANAの方に乗っていただいた時に『スムーズな走行制御ですね』というコメントもいただくことができ、『大変だったけどやり切れてよかった!』と喜びがこみ上げました」(山田)
羽田空港での実証実験も無事に終了。技術面や運用面、空港インフラなどさまざまな観点から課題を抽出することもでき、実用化に向けてさらに大きく前進した。
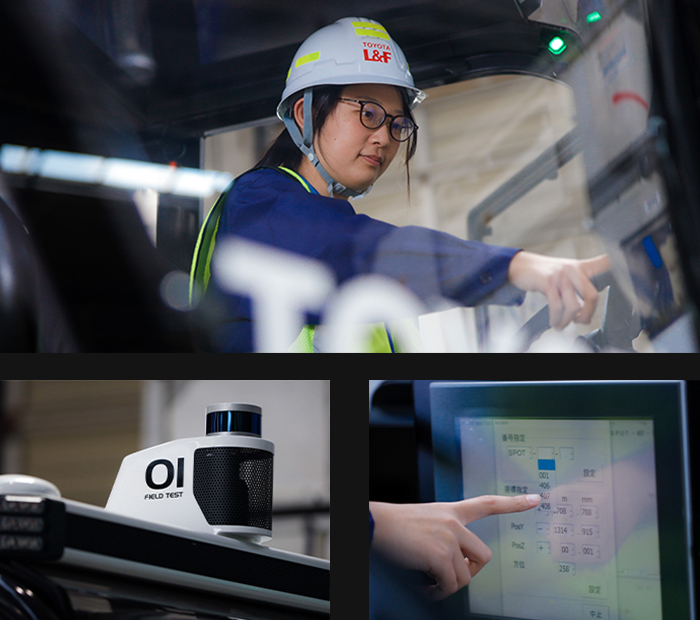
STORY 8
航空業界以外への展開も見据えて
鈴木は本プロジェクトにおいて、ANA・国土交通省航空局との技術渉外を担当した。
「ANA・国土交通省と当社の間に立ち、ご要望を伺ったり、提言したりするのが私の役割。羽田空港の実証実験では、車両だけでは解決できない、空港のインフラ面での課題も見えてきました。そうした課題について今後、開発陣の意見を集約して提言していきたいと考えています」(鈴木)
鈴木は空港で働く人々のニーズを肌で感じることのできる立場でもある。
「佐賀空港、セントレア、羽田空港、それぞれにおける実証実験後に空港内の全事業者さんからアンケートをとりました。『自動化に期待しています』というコメントを多くいただき、ニーズの高さを実感しています」(鈴木)
空港内における無人搬送(自動運転レベル4)の実現目標は2025年。その具現化に向けて開発は今も進められている。また、本プロジェクトで培った知見や技術を、他の空港地上支援業務や航空業界以外に展開することも見据えている。
「航空業界の省力化・省人化のために当社にできること、やるべきことはまだまだたくさんあると、今回のプロジェクトを通じて実感しました」(古橋)
「自動運転トーイングトラクターで培った自律走行技術は、屋内外シームレスに往来可能な自動運転フォークリフトや無人搬送車の開発につなげられると考えています」(望月)
お客さまに新たな価値とソリューションを提供するために、今も一人一人が挑戦を続けている。その先にある「世界の産業・社会基盤を支え、住みよい地球と豊かな生活、そして温かい社会づくり」への貢献を目指して。
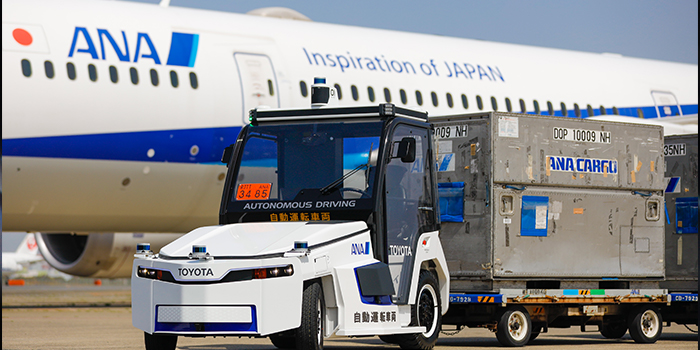